Introduction: Isothermal forging is revolutionizing the production of titanium ingots.
Isothermal forging, a process where both the die and material are maintained at a constant temperature during forging, has emerged as a groundbreaking technology for titanium ingots. Traditionally, titanium has been challenging to forge due to its high reactivity at elevated temperatures and its tendency to become brittle when exposed to extreme thermal cycling. However, the advent of isothermal forging has made it possible to manipulate titanium more efficiently, opening up new possibilities for its use in advanced applications such as aerospace, medical devices, and automotive industries. But why is this process so significant for titanium ingots?
Isothermal forging offers significant advantages over traditional methods, improving the efficiency, quality, and versatility of titanium ingots for high-performance applications.
Let’s delve into the importance of isothermal forging in titanium ingot production and its broader implications for industries reliant on this remarkable metal.
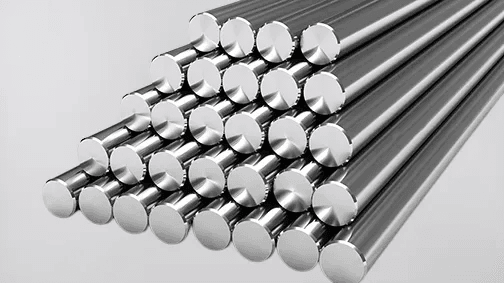
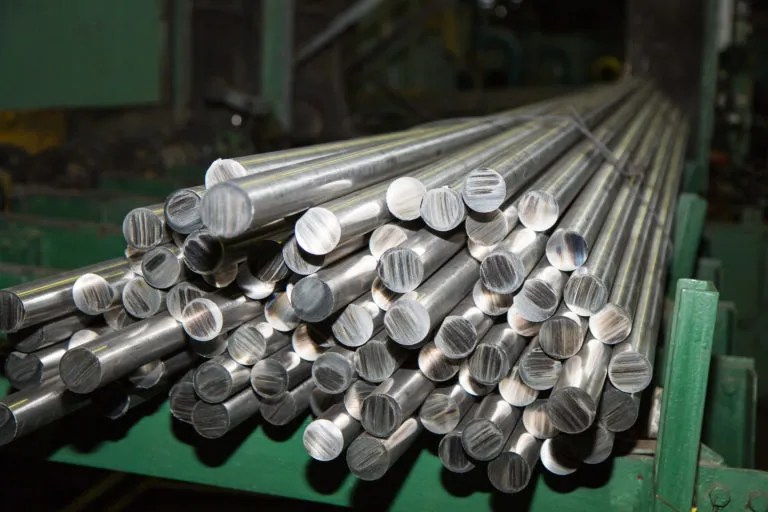
What is Isothermal Forging and How Does It Work?
Isothermal forging is a method that involves forging a material under constant temperature conditions, where both the metal and the die are maintained at the same temperature throughout the process. This is different from traditional forging, where the material undergoes thermal cycling, which can result in inconsistent mechanical properties and potential material degradation.
• Maintaining Uniform Temperature: In isothermal forging, the titanium ingot is heated to a specific temperature, and both the material and the forging die are kept at the same temperature throughout the process. This reduces the temperature fluctuations that typically occur in conventional forging, leading to more consistent material properties.
• Enhanced Control: The key benefit of this technique is that it allows for greater control over the material’s behavior, enabling the production of titanium components with higher precision, better mechanical properties, and improved fatigue resistance. This is particularly important for industries that demand high-quality, reliable titanium products.
Isothermal forging ensures consistent temperature control, improving the quality and mechanical properties of titanium ingots.
How Does Isothermal Forging Improve Titanium’s Workability?
Titanium is a challenging material to forge, particularly at high temperatures. Traditionally, titanium is forged at temperatures between 800°C and 1,200°C, but this can result in high oxidation rates and inconsistencies in the final product. Isothermal forging significantly improves the workability of titanium by:
• Reduced Oxidation: By maintaining a constant temperature, isothermal forging reduces the temperature gradients that can lead to oxidation on the surface of titanium ingots. This is particularly important for titanium, as its surface oxide layer can interfere with the material’s integrity and performance in critical applications.
• Enhanced Plasticity: The consistent temperature helps titanium maintain its plasticity during forging, allowing for more intricate shapes and reduced chances of cracking or breaking. This is particularly crucial when forging high-performance titanium components for industries like aerospace and medical devices.
Isothermal forging allows for better control over oxidation and plasticity, making titanium easier to forge into complex shapes without compromising quality.
How Does Isothermal Forging Impact the Material Properties of Titanium?
Titanium has excellent strength-to-weight ratio, corrosion resistance, and biocompatibility, making it ideal for high-performance applications. However, achieving optimal material properties requires precise control during processing. Isothermal forging plays a crucial role in enhancing these properties:
• Improved Grain Structure: The uniform heating provided by isothermal forging results in a more uniform grain structure, improving the mechanical properties of titanium. This leads to enhanced strength, toughness, and fatigue resistance, which is vital for components used in critical applications such as aircraft engines or medical implants.
• Better Ductility and Toughness: The consistent temperature during forging ensures that titanium retains its ductility and toughness, essential for reducing the risk of failure under stress. This is especially beneficial when producing titanium components that will undergo complex mechanical stress in service.
Isothermal forging enhances the grain structure and mechanical properties of titanium, improving strength, toughness, and fatigue resistance.
How Does Isothermal Forging Contribute to Cost Efficiency in Titanium Ingot Production?
Titanium is known for being an expensive material due to its extraction process and high manufacturing costs. Isothermal forging can help reduce the overall cost of producing titanium ingots by:
• Reducing Material Waste: Traditional forging processes often result in significant material waste due to the need for higher temperature gradients and the risk of defects. Isothermal forging minimizes these issues by ensuring more uniform deformation and reducing the need for costly material rework.
• Faster Production Cycles: The precision and uniformity of isothermal forging enable faster production cycles, which can lower labor and energy costs. As the process is more controlled, manufacturers can achieve higher yields per cycle, reducing the cost of titanium ingots over time.
• Lower Energy Consumption: Since isothermal forging keeps the material at a constant temperature, it often requires less energy compared to traditional forging, where large amounts of energy are needed to heat the material and die to different temperatures.
Isothermal forging reduces material waste and production time, resulting in significant cost savings in the titanium ingot production process.
How Does Isothermal Forging Open Up New Applications for Titanium?
Titanium is a versatile metal with numerous applications, but its processing challenges have limited its use in some industries. With the advent of isothermal forging, titanium is now more suitable for producing components in a wider range of industries:
• Aerospace Industry: Titanium is crucial in aerospace applications due to its strength-to-weight ratio. Isothermal forging allows for the production of highly complex, high-performance components like turbine blades and structural parts with superior mechanical properties.
• Medical Industry: The biocompatibility and strength of titanium make it ideal for medical implants. Isothermal forging allows for the production of customized medical devices that require precise and consistent mechanical properties, improving the safety and effectiveness of implants and prosthetics.
• Automotive Industry: The automotive industry is increasingly using titanium for lightweight, high-performance parts, and isothermal forging helps produce these parts more efficiently, leading to improved fuel efficiency and reduced emissions in vehicles.
Isothermal forging enables titanium to be used in a broader range of industries, enhancing the material’s versatility for complex and high-performance applications.
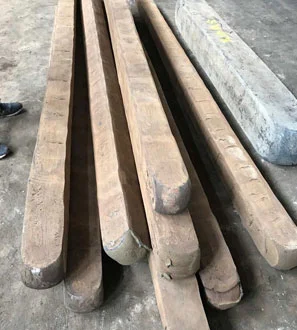
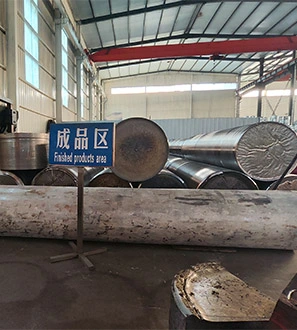
How Does Isothermal Forging Contribute to Sustainability in Titanium Production?
Sustainability is becoming increasingly important in manufacturing processes, and isothermal forging can help improve the environmental footprint of titanium production:
• Reduced Material Waste: The precision of isothermal forging results in less material waste, which is not only cost-effective but also environmentally beneficial. By optimizing the material usage, manufacturers can reduce the demand for titanium extraction and minimize the environmental impact associated with material waste.
• Energy Efficiency: The reduced energy consumption in isothermal forging translates to a smaller carbon footprint, making the process more environmentally friendly. This contributes to the growing demand for greener, more sustainable manufacturing practices in the titanium industry.
Isothermal forging contributes to sustainability by reducing waste and energy consumption, making titanium production more eco-friendly.
Claim: Isothermal Forging is Revolutionizing Titanium Ingot Production
The introduction of isothermal forging has made a significant impact on the production of titanium ingots, offering advantages such as improved material properties, greater efficiency, and reduced costs. By allowing for more precise control over temperature, isothermal forging enhances the overall quality and functionality of titanium components, making it ideal for high-performance applications.
Conclusion: Isothermal Forging is the Future of Titanium Ingot Production
As we look to the future, I believe that isothermal forging will play an increasingly important role in the production of titanium ingots. Its ability to improve material properties, reduce waste, and open up new possibilities for titanium’s use in critical industries makes it a game-changer. This technology is setting the stage for a more efficient, cost-effective, and versatile future for titanium manufacturing.