Introduction: Advancing Titanium Forging Technology
Titanium forging technology is at the forefront of material science, with innovations aimed at improving efficiency, reducing costs, and expanding applications. As industries demand more from materials, the field of titanium forging continues to evolve, incorporating advanced processes and techniques to meet these challenges. But what are the key innovations transforming this space?
Emerging advancements in titanium forging technology include isothermal forging, additive manufacturing integration, and AI-driven process optimization, all contributing to better performance and cost efficiency.
Let me guide you through the groundbreaking innovations shaping the future of titanium forging.
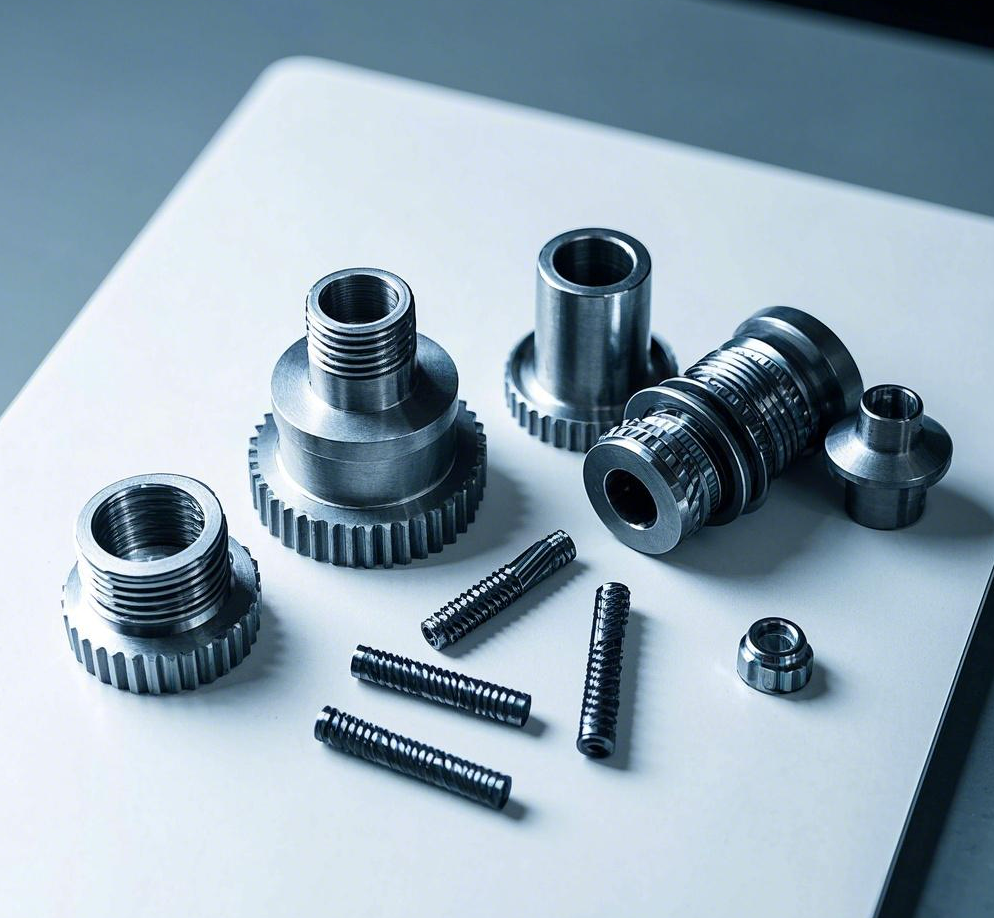
How Is Isothermal Forging Revolutionizing Titanium Production?
Isothermal forging involves maintaining constant temperature conditions for both the titanium and the die, improving material properties and precision.
Key benefits:
• Enhanced Material Integrity: Prevents thermal gradients that can cause defects or uneven grain flow.
• Improved Strength and Fatigue Resistance: Ensures uniform mechanical properties.
• Application Versatility: Used in critical aerospace and medical applications where precision is paramount.
Isothermal forging is one of the most exciting advancements, offering unmatched control over the forging process.
How Does Additive Manufacturing Integrate with Forging?
The combination of 3D printing and forging technology is unlocking new possibilities in titanium production.
Key advancements:
• Hybrid Manufacturing: Additive manufacturing creates near-net shapes, which are then forged for superior mechanical properties.
• Material Efficiency: Reduces waste by using only the required material, especially in high-cost titanium.
• Complex Geometries: Enables the production of intricate designs that were previously impossible with traditional forging alone.
This integration represents a powerful synergy that enhances design freedom and cost efficiency.
What Role Does AI Play in Titanium Forging Optimization?
Artificial intelligence is transforming titanium forging by analyzing data and optimizing processes in real time.
Key innovations:
• Predictive Maintenance: AI monitors equipment health to prevent downtime and ensure consistent quality.
• Process Simulation: Advanced algorithms simulate forging conditions to refine parameters and reduce defects.
• Cost Reduction: Optimized workflows minimize energy use and material waste.
AI-driven insights are enabling smarter, more sustainable production practices.
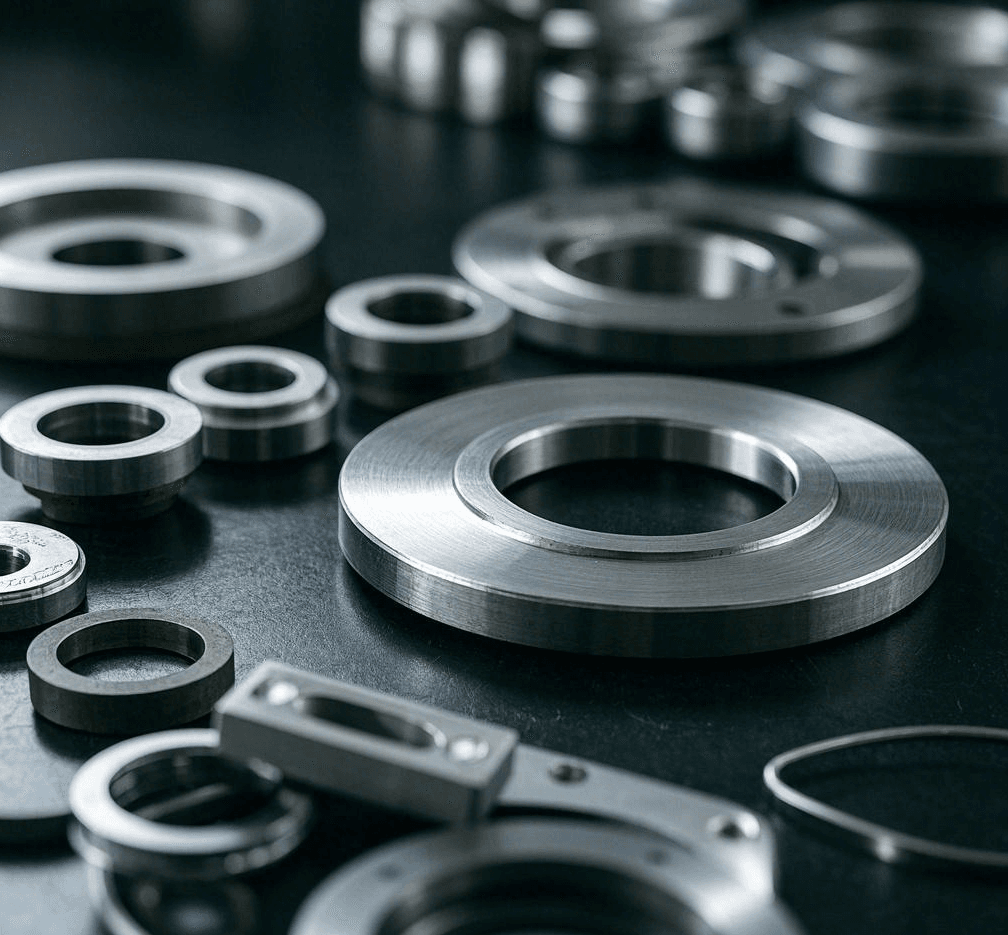
How Are New Alloys Expanding Titanium Forging Applications?
Research into titanium alloys is unlocking new applications by enhancing specific properties like strength, heat resistance, and corrosion resistance.
Examples include:
• Beta Titanium Alloys: Improved ductility and formability for applications like automotive springs and aerospace components.
• Titanium-Matrix Composites: Reinforced with ceramic or other materials for extreme wear resistance.
• High-Temperature Alloys: Tailored for jet engines and power generation.
For me, these alloys demonstrate how innovation in materials science can redefine what titanium forgings can achieve.
How Are Sustainable Practices Shaping Titanium Forging?
Sustainability is a growing focus, with innovations aimed at reducing the environmental impact of titanium forging.
Key developments:
• Energy-Efficient Processes: Techniques like near-net-shape forging reduce the energy required for material shaping.
• Recycling Programs: Closed-loop systems reclaim titanium scrap for reuse, minimizing waste.
• Eco-Friendly Coatings: Eliminate the need for environmentally harmful surface treatments.
These sustainable practices not only align with global environmental goals but also reduce costs in the long term.
What Are the Advances in Precision Forging Techniques?
Precision forging is evolving to produce components with tighter tolerances and less post-processing.
Key innovations:
• Near-Net-Shape Forging: Reduces material waste and machining time.
• Advanced Die Materials: Extend tool life and improve accuracy.
• Integrated Inspection Systems: Real-time monitoring ensures dimensional accuracy during forging.
Precision forging advancements are paving the way for titanium’s use in highly specialized applications, from aerospace to medical devices.
Claim: Why Innovation Is Driving Titanium Forging Forward
Emerging technologies like isothermal forging, AI optimization, and hybrid manufacturing are revolutionizing the titanium forging industry. These innovations enhance material performance, expand application possibilities, and drive efficiency in production.
Conclusion: Shaping the Future of Titanium Forging
As I reflect on the advancements in titanium forging, I see a field that’s evolving rapidly to meet the demands of modern industries. From integrating AI to creating hybrid manufacturing techniques, each innovation pushes the boundaries of what titanium can achieve. Personally, I find these developments not just inspiring but essential for addressing the challenges of tomorrow. In a world that demands more from materials, titanium forging stands as a testament to human ingenuity and the pursuit of excellence.