Introduction: The Complexity of Titanium Forging Production
Titanium forgings are essential for industries requiring lightweight strength, corrosion resistance, and durability. However, producing high-quality titanium forgings is no simple task. Manufacturers must overcome material-specific challenges, as well as technical and economic hurdles, to meet the demanding standards of aerospace, medical, and industrial applications. But what are these challenges, and how do they impact production?
Producing titanium forgings presents challenges such as high material costs, difficult machinability, and precise temperature control, all of which require specialized techniques and equipment.
Let me explain the common obstacles manufacturers face and their implications for production efficiency and quality.
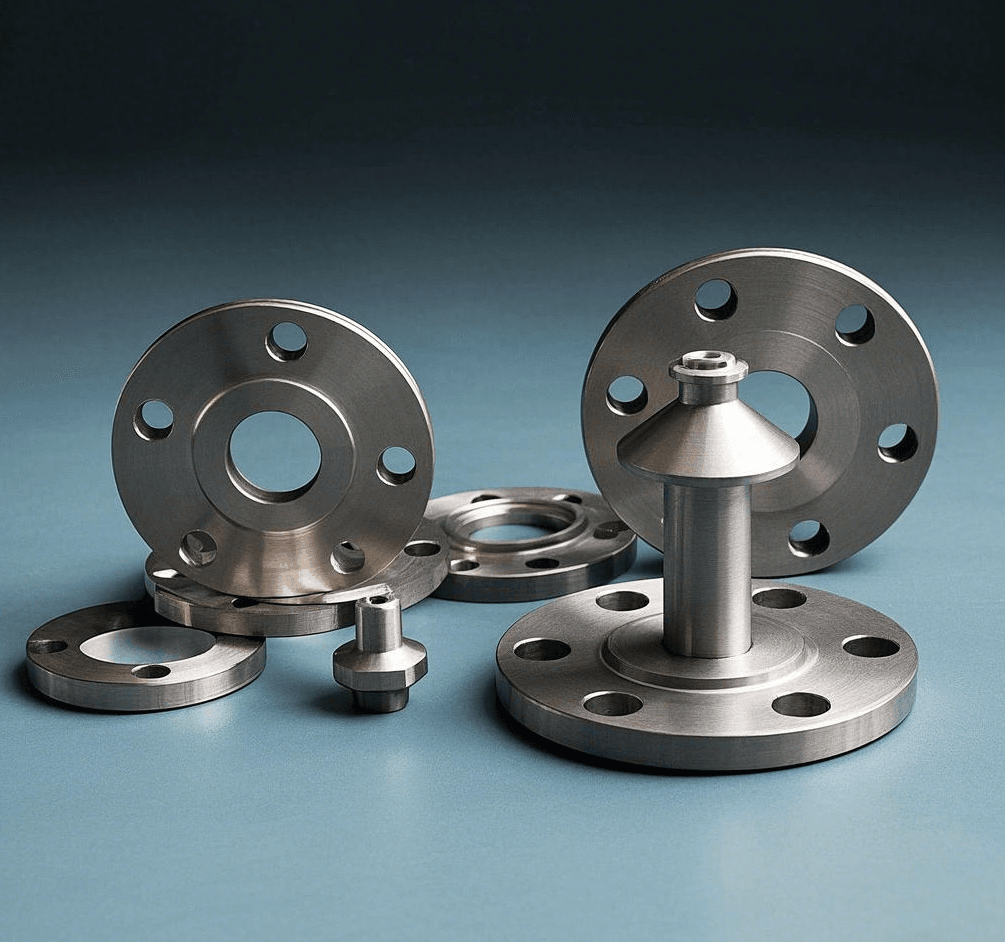
How Do High Material Costs Affect Titanium Forging?
Titanium is an expensive raw material, and its production process—from mining to forging—adds significant costs.
Key issues include:
• Raw Material Expense: Titanium ore is costly to extract and refine, contributing to higher initial costs.
• Material Wastage: Forging processes, especially open-die forging, can generate significant scrap material, further increasing expenses.
• Economic Viability: High costs can deter manufacturers and clients from using titanium unless its benefits outweigh the expense.
For me, managing material waste and optimizing processes are critical to minimizing costs and maintaining competitiveness.
Why Is Temperature Control Crucial in Titanium Forging?
Titanium’s sensitivity to temperature makes precise control essential throughout the forging process.
Key challenges include:
• Narrow Working Range: Titanium must be heated within a specific temperature range (usually 800–950°C) to prevent cracking or oxidation.
• Risk of Overheating: Excessive heat can degrade mechanical properties and lead to defects.
• Equipment Demands: Maintaining precise temperature requires advanced furnaces and monitoring systems, increasing production complexity.
For me, achieving precise temperature control is the foundation for producing high-quality titanium forgings.
How Does Titanium’s Poor Machinability Impact Production?
Titanium is notoriously difficult to machine due to its high strength and low thermal conductivity.
Key difficulties:
• Tool Wear: Cutting tools wear out quickly when machining titanium, driving up costs and downtime.
• Heat Buildup: Poor heat dissipation can cause work hardening, affecting surface quality and increasing machining time.
• Surface Defects: Achieving smooth, defect-free surfaces requires specialized tools and techniques.
For me, addressing these machining challenges is essential to ensure precision and minimize production delays.
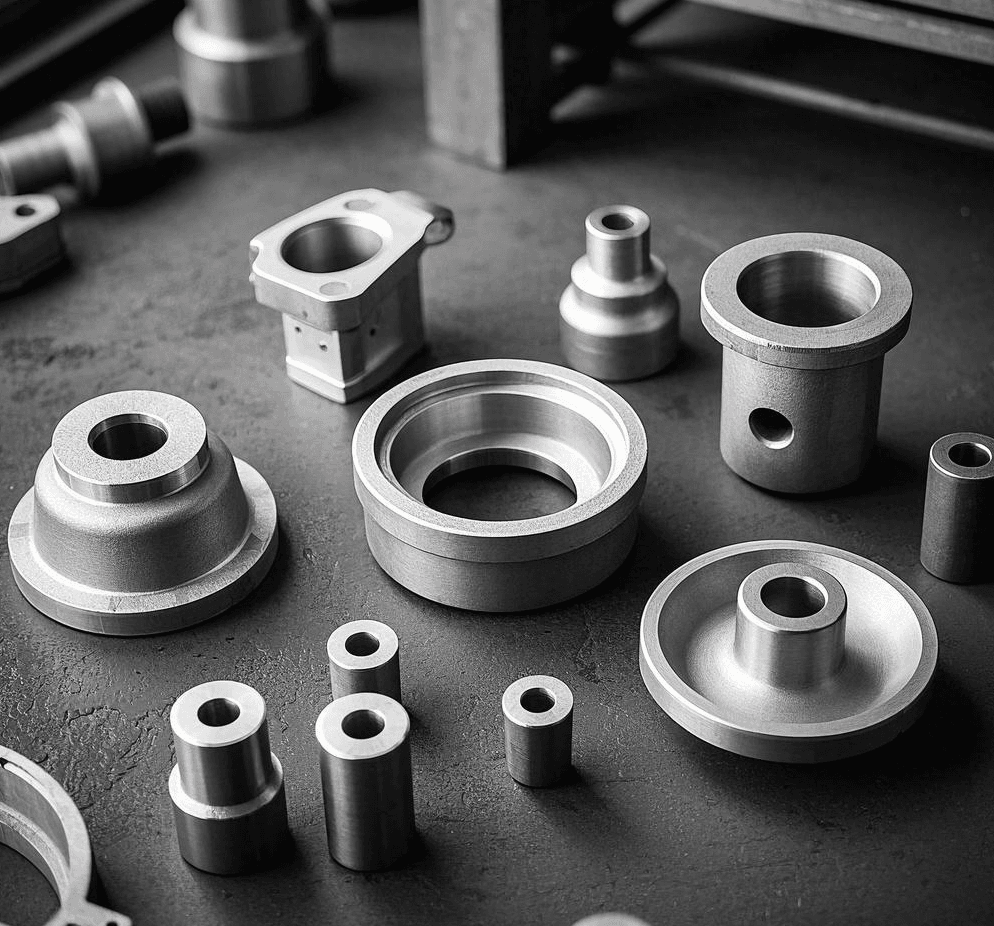
How Does Oxidation Affect Titanium Forgings?
Titanium is highly reactive at elevated temperatures, leading to challenges with oxidation and contamination.
Key concerns include:
• Alpha-Case Formation: At high temperatures, a brittle oxide layer (alpha case) can form on the surface, compromising mechanical properties.
• Protective Atmospheres: Forging often requires inert gas environments (like argon) to prevent oxidation, increasing production costs.
For me, controlling oxidation is critical for preserving the integrity and performance of forged titanium components.
What Challenges Arise in Forging Complex Titanium Shapes?
Titanium’s high strength and limited ductility make it difficult to forge into intricate or detailed shapes.
Key obstacles:
• Tooling Requirements: Producing complex shapes requires precise dies, which can be expensive and time-consuming to manufacture.
• Risk of Cracking: Titanium’s limited flexibility at lower temperatures increases the risk of cracks during forging.
• Consistency Issues: Ensuring uniformity in large or complex components is challenging, requiring careful process optimization.
For me, achieving design complexity without sacrificing quality is a delicate balance that requires expertise and advanced equipment.
How Do Environmental and Safety Concerns Impact Production?
The production of titanium forgings involves processes that pose environmental and safety challenges.
Key concerns:
• Energy Intensity: High temperatures and specialized equipment consume significant energy, raising sustainability issues.
• Fire Risk: Titanium powder and chips are flammable, requiring strict handling and storage procedures.
• Waste Management: Recycling and disposal of titanium scrap demand additional resources and planning.
For me, prioritizing safety and sustainability is essential for responsible and efficient production.
Claim: Why Producing Titanium Forgings Is Challenging
Manufacturing titanium forgings is a complex process requiring precise temperature control, advanced machining techniques, and careful waste management. These challenges, combined with high costs and technical demands, highlight the expertise and innovation needed to produce high-quality components.
Conclusion: Overcoming Challenges in Titanium Forging
Producing titanium forgings is not without its difficulties, but these challenges underscore the material’s exceptional properties and importance in critical applications. For me, navigating these obstacles requires a commitment to innovation, precision, and sustainability. By mastering these complexities, manufacturers can deliver titanium forgings that redefine performance and reliability across industries.