Introduction
Titanium is a crucial material in the marine industry due to its excellent resistance to seawater corrosion, high strength-to-weight ratio, and long-term durability. These properties make titanium an ideal choice for a variety of marine applications, ensuring reliable performance in challenging oceanic environments.
In this article, we explore the various applications of titanium in the marine industry, detailing the benefits it provides and why it is a preferred material for many marine structures and systems.
Features of Titanium
Titanium offers several key features that make it particularly suitable for marine applications:
- Seawater Corrosion Resistance: Titanium’s resistance to corrosion from seawater makes it an ideal material for marine applications where exposure to harsh, saline environments is inevitable.
- High Strength-to-Weight Ratio: Titanium is strong yet lightweight, making it easy to handle and install, particularly in marine vessels and underwater structures.
- Durability in Harsh Environments: Titanium’s ability to withstand harsh oceanic conditions ensures a long lifespan for marine equipment, reducing the need for frequent replacements.
- Non-Magnetic Properties: Titanium’s non-magnetic properties make it suitable for applications where magnetic interference must be minimized, such as in submarines and naval vessels.
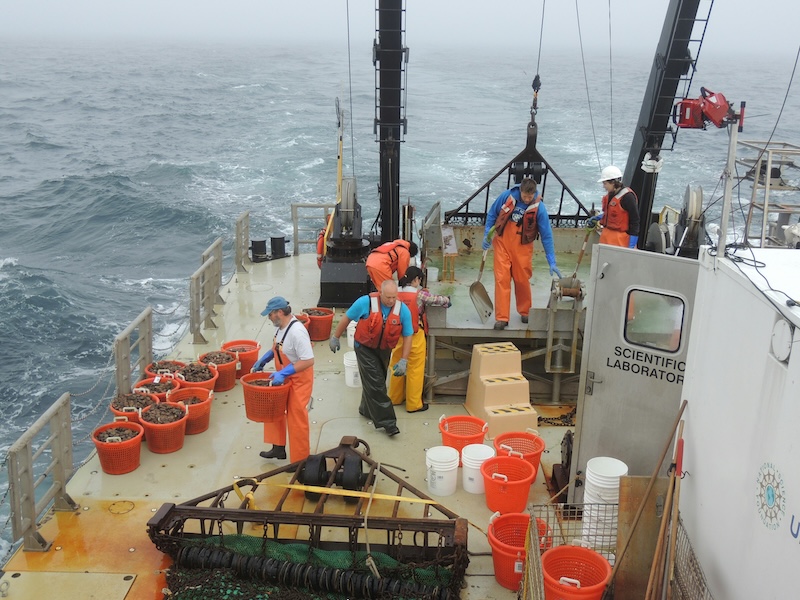
The Most Commonly Used Grades of Titanium in Marine Applications
- Grade 2 Titanium: Grade 2 titanium is commercially pure and offers excellent resistance to seawater corrosion, making it ideal for use in marine piping, heat exchangers, and other submerged equipment.
- Grade 5 Titanium (Ti-6Al-4V): Grade 5 titanium provides higher strength compared to commercially pure grades, making it suitable for high-stress marine components, such as propeller shafts and structural elements.
Advantages of Titanium in Marine Applications
The use of titanium in marine applications provides several notable advantages:
- Corrosion Resistance: Titanium’s ability to resist seawater corrosion ensures the long-term durability of marine equipment, even in highly saline environments.
- Weight Reduction: Titanium’s lightweight properties reduce the overall weight of marine vessels and components, contributing to better fuel efficiency and maneuverability.
- Long-Term Durability: Titanium’s durability in the face of harsh marine conditions helps extend the lifespan of equipment, reducing the need for maintenance and replacement.
Key Applications of Titanium in the Marine Industry
Titanium is used in a variety of marine applications, including:
- Propeller Shafts: Titanium is used in propeller shafts due to its high strength and excellent corrosion resistance, providing reliable performance and reducing maintenance needs.
- Heat Exchangers and Condensers: Titanium is used in heat exchangers and condensers for seawater cooling systems on ships and marine platforms. Its resistance to seawater corrosion ensures efficient heat transfer and long-lasting equipment performance.
- Seawater Piping Systems: Titanium piping systems are used for transporting seawater in marine vessels, offering corrosion resistance and reducing the risk of leaks or blockages caused by corrosion.
- Submarine Components: Titanium’s non-magnetic properties make it an ideal choice for submarine hulls and components, helping to reduce magnetic signature and avoid detection.
- Offshore Oil and Gas Platforms: Titanium is used in offshore oil and gas platforms for risers, piping, and structural components due to its corrosion resistance and durability in the harsh marine environment.
Comparisons: Titanium vs. Other Materials in Marine Applications
Titanium is often compared to other materials used in marine applications, such as stainless steel, aluminum, and copper alloys:
- Titanium vs. Stainless Steel: Stainless steel is commonly used in marine applications, but titanium offers superior resistance to seawater corrosion, particularly in environments where chlorides are present.
- Titanium vs. Aluminum: Aluminum is lightweight and corrosion-resistant but lacks the strength of titanium, making titanium preferable for high-stress applications such as propeller shafts and structural components.
- Titanium vs. Copper Alloys: Copper alloys, such as bronze, are used in marine applications, but titanium’s superior corrosion resistance and strength make it a more durable choice for long-term exposure to seawater.
Benefits of Using Titanium in Marine Applications
The benefits of using titanium in marine applications are numerous:
- Extended Equipment Lifespan: Titanium’s resistance to seawater corrosion ensures that marine equipment remains functional for longer, reducing the need for replacements.
- Lower Maintenance Costs: Titanium’s durability and resistance to corrosion minimize the need for frequent maintenance, leading to lower operational costs.
- Improved Vessel Performance: Titanium’s lightweight properties contribute to better fuel efficiency and maneuverability for marine vessels, improving overall performance.
Challenges in Using Titanium in Marine Applications
Despite its advantages, there are challenges associated with using titanium in marine applications:
- High Cost: Titanium is more expensive compared to other materials, such as stainless steel and aluminum, which can limit its use in some marine applications.
- Machining Difficulty: Titanium’s hardness makes it challenging to machine, requiring specialized equipment and techniques, which can increase production costs and complexity.
Future Trends for Titanium in Marine Applications
The use of titanium in the marine industry is expected to grow as advancements in alloy production and manufacturing techniques make it more cost-effective. Emerging trends include the use of titanium in more specialized marine applications, such as autonomous underwater vehicles (AUVs) and deep-sea exploration equipment, where its corrosion resistance and lightweight properties are crucial. Innovations in welding and fabrication are also expected to make titanium more accessible for large-scale marine structures.
FAQs about Titanium in Marine Applications
- Why is titanium used in marine applications?
- Titanium is used due to its excellent resistance to seawater corrosion, high strength, and lightweight properties, making it ideal for marine applications.
- What types of marine equipment use titanium?
- Titanium is used in propeller shafts, heat exchangers, seawater piping systems, submarine components, and offshore oil and gas platforms.
- How does titanium enhance the performance of marine vessels?
- Titanium’s lightweight properties reduce the overall weight of marine vessels, improving fuel efficiency and maneuverability.
- Is titanium used in submarine components?
- Yes, titanium is used in submarine components due to its non-magnetic properties, which help reduce the vessel’s magnetic signature.
- What are the advantages of titanium over stainless steel in marine applications?
- Titanium offers superior resistance to seawater corrosion, particularly in environments containing chlorides, making it a more durable choice for marine applications.
- Can titanium be used for heat exchangers on ships?
- Yes, titanium is used in heat exchangers for seawater cooling systems on ships due to its ability to resist seawater corrosion and maintain efficient heat transfer.
- What challenges are associated with using titanium in marine applications?
- The main challenges include the high cost of titanium and the difficulty in machining it for complex marine components.
- How does titanium improve the efficiency of offshore oil and gas platforms?
- Titanium’s corrosion resistance and lightweight properties contribute to reduced maintenance needs and improved structural efficiency on offshore platforms.
- Why is titanium suitable for seawater piping systems?
- Titanium’s resistance to corrosion from seawater ensures the long-term reliability of piping systems used for transporting seawater on marine vessels.
- Is titanium used in autonomous underwater vehicles (AUVs)?
- Yes, titanium is increasingly used in AUVs due to its corrosion resistance, lightweight nature, and durability in deep-sea environments.
- How does titanium compare to aluminum in marine applications?
- While aluminum is corrosion-resistant and lightweight, titanium offers greater strength, making it preferable for high-stress components such as propeller shafts.
- What future developments are expected for titanium in the marine industry?
- Advances in alloy production and welding techniques are expected to make titanium more cost-effective, expanding its use in specialized marine applications.
- Can titanium withstand deep-sea conditions?
- Yes, titanium’s resistance to corrosion and durability make it suitable for deep-sea conditions, ensuring reliable performance in extreme environments.
- Why is titanium used in offshore oil and gas platforms?
- Titanium’s corrosion resistance and strength make it ideal for use in risers, piping, and structural components on offshore platforms, where harsh marine conditions are common.
- How does titanium contribute to lower maintenance costs in marine applications?
- Titanium’s resistance to seawater corrosion reduces the need for frequent maintenance, leading to lower operational costs for marine vessels and structures.
Conclusion
Titanium’s unique properties make it an ideal material for use in the marine industry. Its resistance to seawater corrosion, lightweight strength, and long-term durability make it invaluable for a wide range of marine applications, from propeller shafts and piping systems to submarine components and offshore platforms. Despite challenges related to cost and machining, the benefits of using titanium in marine applications far outweigh the drawbacks, ensuring its continued use and expanding role in the future of marine technology.