Introduction
Titanium is a critical material in the aerospace industry due to its unique properties, such as high strength-to-weight ratio, excellent corrosion resistance, and high-temperature tolerance. These features make titanium an ideal choice for a wide range of aerospace applications, contributing to improved performance, safety, and fuel efficiency in aircraft and spacecraft.
In this article, we explore the various applications of titanium in the aerospace industry, highlighting the benefits it provides and why it is the preferred material for many aerospace components.
Features of Titanium
Titanium offers several key features that make it particularly suitable for aerospace applications:
- High Strength-to-Weight Ratio: Titanium’s combination of strength and low weight makes it particularly suitable for aerospace applications where weight reduction is crucial.
- Corrosion Resistance: Titanium is highly resistant to corrosion from environmental factors, ensuring that components remain intact and functional for long periods.
- High-Temperature Tolerance: Titanium can withstand extreme temperatures, making it ideal for use in engines and other high-temperature areas of aircraft.
- Fatigue Resistance: Titanium has excellent fatigue resistance, which is critical in aerospace applications that are subject to repeated loading and unloading cycles.
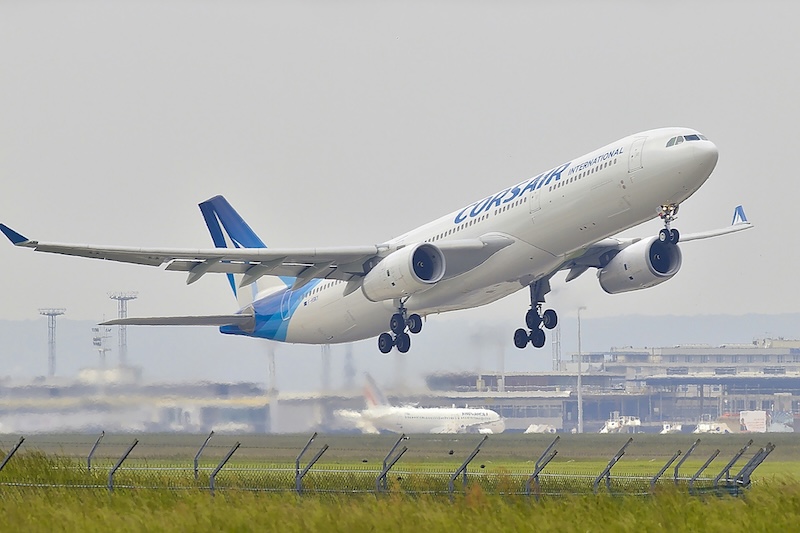
The Most Commonly Used Grades of Titanium in Aerospace Applications
- Grade 5 Titanium (Ti-6Al-4V): Grade 5 titanium is an alloy that provides high strength, excellent corrosion resistance, and good weldability, making it ideal for structural components and engine parts.
- Grade 9 Titanium (Ti-3Al-2.5V): Grade 9 titanium is a lighter and more formable alloy, suitable for applications such as hydraulic tubing and aircraft skins where strength and formability are needed.
Advantages of Titanium in Aerospace Applications
The use of titanium in aerospace applications provides several notable advantages:
- Weight Reduction: Titanium’s lightweight properties contribute to reduced overall aircraft weight, which enhances fuel efficiency and extends flight range.
- Durability in Harsh Environments: Titanium’s resistance to corrosion and high temperatures ensures that aerospace components remain reliable in extreme conditions, improving safety and performance.
- High Strength: Titanium’s strength allows it to be used in critical load-bearing components, providing structural integrity without adding significant weight.
Key Applications of Titanium in the Aerospace Industry
Titanium is used in a wide range of aerospace applications, including:
- Aircraft Structures: Titanium is used in the structural components of aircraft, including frames, wings, and landing gear, due to its strength and ability to withstand the stresses of flight.
- Engine Components: Titanium is used in jet engine components, such as compressor blades, casings, and discs, where high strength and heat resistance are required.
- Hydraulic Systems: Titanium tubing is used in hydraulic systems of aircraft, where weight reduction and resistance to corrosion are crucial for performance and reliability.
- Exhaust Systems: Titanium is used in exhaust systems due to its high-temperature tolerance, ensuring that components can handle the extreme heat generated by jet engines.
- Fasteners: Titanium fasteners are used extensively in aerospace applications to hold various components together while keeping the weight low.
Comparisons: Titanium vs. Other Materials in Aerospace Applications
Titanium is often compared to other materials used in aerospace applications, such as aluminum, steel, and composites:
- Titanium vs. Aluminum: Aluminum is commonly used in aerospace due to its lightweight properties, but titanium offers superior strength and temperature resistance, making it preferable for components that experience high stress or extreme heat.
- Titanium vs. Steel: Steel is strong but significantly heavier than titanium. Titanium provides comparable strength at a fraction of the weight, making it ideal for weight-sensitive aerospace applications.
- Titanium vs. Composites: Composites are lightweight and corrosion-resistant, but titanium provides better impact resistance and is often used in conjunction with composites for added structural integrity.
Benefits of Using Titanium in Aerospace Applications
The benefits of using titanium in aerospace applications are numerous:
- Fuel Efficiency: The use of titanium in aircraft helps reduce overall weight, leading to improved fuel efficiency and extended flight range.
- Increased Safety: Titanium’s high strength and fatigue resistance contribute to the structural integrity of aircraft, enhancing overall safety.
- Long-Term Durability: Titanium’s resistance to corrosion and ability to withstand high temperatures ensure that aerospace components have a long operational life, reducing maintenance needs.
Challenges in Using Titanium in Aerospace Applications
Despite its advantages, there are challenges associated with using titanium in aerospace applications:
- High Cost: Titanium is more expensive compared to materials like aluminum, which can limit its use in certain aerospace applications.
- Machining Difficulty: Titanium’s hardness makes it challenging to machine, requiring specialized tools and techniques that can increase production costs.
Future Trends for Titanium in Aerospace Applications
The use of titanium in the aerospace industry is expected to grow as advancements in production techniques and alloy development make it more cost-effective. Emerging trends include the use of titanium in additive manufacturing, allowing for the production of complex, lightweight components with minimal material waste. Titanium’s role in next-generation aircraft and space exploration vehicles is also expected to expand, with a focus on improving performance and fuel efficiency.
FAQs about Titanium in Aerospace Applications
- Why is titanium used in aerospace applications?
- Titanium is used due to its high strength-to-weight ratio, corrosion resistance, and ability to withstand extreme temperatures, making it ideal for aerospace components.
- What types of aerospace components use titanium?
- Titanium is used in aircraft structures, engine components, hydraulic systems, exhaust systems, and fasteners.
- How does titanium contribute to fuel efficiency in aircraft?
- Titanium’s lightweight properties help reduce the overall weight of aircraft, leading to improved fuel efficiency and extended flight range.
- Is titanium used in jet engines?
- Yes, titanium is used in jet engine components such as compressor blades and casings due to its high strength and heat resistance.
- What are the advantages of titanium over aluminum in aerospace applications?
- Titanium offers superior strength and high-temperature resistance compared to aluminum, making it preferable for high-stress or heat-exposed components.
- Can titanium be used in exhaust systems?
- Yes, titanium is used in exhaust systems because of its ability to withstand the extreme heat generated by jet engines.
- What challenges are associated with using titanium in aerospace applications?
- The main challenges include the high cost of titanium and the difficulty in machining it for complex aerospace components.
- How does titanium improve the safety of aircraft?
- Titanium’s high strength and fatigue resistance enhance the structural integrity of aircraft, reducing the risk of failure and improving overall safety.
- Why is titanium suitable for hydraulic systems in aircraft?
- Titanium’s corrosion resistance and lightweight nature make it ideal for hydraulic systems, ensuring long-term reliability and performance.
- Is titanium used in space exploration vehicles?
- Yes, titanium is used in space exploration vehicles due to its high strength, lightweight properties, and ability to withstand the extreme conditions of space.
- How does titanium compare to steel in aerospace applications?
- Titanium provides comparable strength to steel but at a significantly lower weight, making it more suitable for weight-sensitive aerospace components.
- What future developments are expected for titanium in aerospace?
- Advances in additive manufacturing and alloy production are expected to make titanium more cost-effective, expanding its use in next-generation aerospace components.
- Can titanium withstand the conditions in jet engines?
- Yes, titanium’s high-temperature tolerance makes it suitable for use in jet engine components that are exposed to extreme heat.
- Why is titanium used in fasteners for aircraft?
- Titanium fasteners are lightweight and strong, helping to hold components together without adding unnecessary weight to the aircraft.
- How does titanium contribute to the longevity of aerospace components?
- Titanium’s resistance to corrosion and fatigue ensures that aerospace components remain functional for long periods, reducing the need for frequent replacements.
Conclusion
Titanium’s unique properties make it an ideal material for use in the aerospace industry. Its high strength-to-weight ratio, corrosion resistance, and ability to withstand extreme temperatures make it invaluable for a wide range of aerospace applications, from aircraft structures and engine components to fasteners and hydraulic systems. Despite challenges related to cost and machining, the benefits of using titanium in aerospace applications far outweigh the drawbacks, ensuring its continued use and expanding role in the future of aviation and space exploration.