Introduction: The Game-Changing Role of Titanium in 3D Printing
In the fast-evolving world of 3D printing, the choice of material is crucial. Titanium has emerged as a revolutionary material, enabling advanced manufacturing solutions across industries like aerospace, healthcare, and automotive. But what makes titanium such a powerful material for 3D printing?
Titanium offers unmatched strength, lightweight properties, and biocompatibility, allowing for highly precise and durable 3D-printed components. Its unique properties make it ideal for critical applications, from medical implants to aerospace parts, where performance and durability are essential.
Below, I’ll dive into the specific ways titanium is transforming 3D printing and why it’s becoming the material of choice for complex, high-performance applications.
How Does Titanium’s Lightweight Strength Benefit Aerospace 3D Printing?
In aerospace, reducing weight without sacrificing strength is essential. Titanium’s high strength-to-weight ratio makes it perfect for 3D-printed parts in aircraft, where every gram matters.
Advantages in Aerospace:
• Improved Fuel Efficiency: Titanium’s lightweight properties help reduce the overall weight of aircraft, resulting in better fuel efficiency and lower emissions.
• Durable and Reliable: 3D-printed titanium parts can withstand high-stress environments, making them ideal for jet engines, landing gear, and structural components.
In my experience, titanium 3D printing in aerospace has been revolutionary, allowing for lighter, more fuel-efficient aircraft components that maintain their structural integrity.
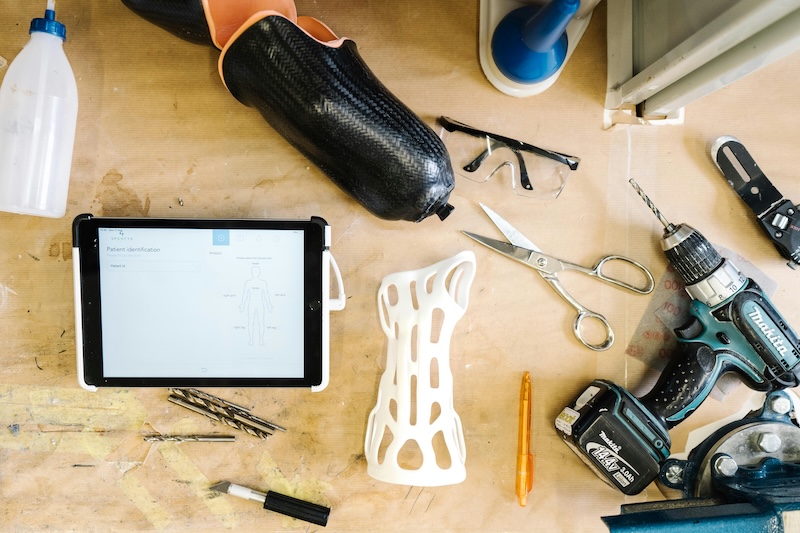
Why Is Titanium’s Biocompatibility Essential for Medical 3D Printing?
Titanium’s biocompatibility makes it safe for use in the human body, which is why it’s widely used in 3D printing for medical applications. This quality is invaluable for producing patient-specific implants and devices.
Advantages in Healthcare:
• Safe for Implants: Titanium’s compatibility with body tissues makes it ideal for implants, reducing the risk of rejection or complications.
• Customizable Solutions: 3D printing with titanium allows me to produce implants tailored to each patient, enhancing fit, comfort, and functionality.
Using titanium for medical 3D printing has opened up new possibilities for personalized patient care, allowing for custom-fit implants that improve recovery times and comfort.
How Does Titanium Enable High-Performance Automotive Parts Through 3D Printing?
In the automotive industry, titanium’s strength and lightness allow for high-performance components that improve efficiency and safety. 3D printing these parts with titanium provides the flexibility to create complex designs.
Advantages in Automotive:
• Enhanced Fuel Efficiency: Lightweight titanium parts reduce vehicle weight, resulting in better fuel efficiency and handling.
• Improved Performance and Safety: Titanium’s strength contributes to the durability of parts like engine components and brake systems, which are critical to vehicle performance and safety.
With titanium, I can 3D print intricate automotive parts that deliver superior performance while reducing vehicle weight, offering clear benefits in both efficiency and driving dynamics.
Why Is Titanium’s Corrosion Resistance Valuable for Marine 3D Printing?
Marine environments are challenging for metals due to constant exposure to saltwater and humidity, which cause corrosion. Titanium’s natural corrosion resistance makes it an ideal material for 3D-printed marine applications.
Advantages in Marine Industry:
• Durability in Saltwater Environments: Titanium remains rust-free in saltwater, extending the lifespan of marine parts like propellers and hull components.
• Low Maintenance Needs: Titanium’s resistance to corrosion reduces the need for frequent maintenance, saving time and costs.
For marine applications, titanium’s corrosion resistance has been invaluable, allowing 3D-printed parts to withstand harsh ocean conditions without degradation.
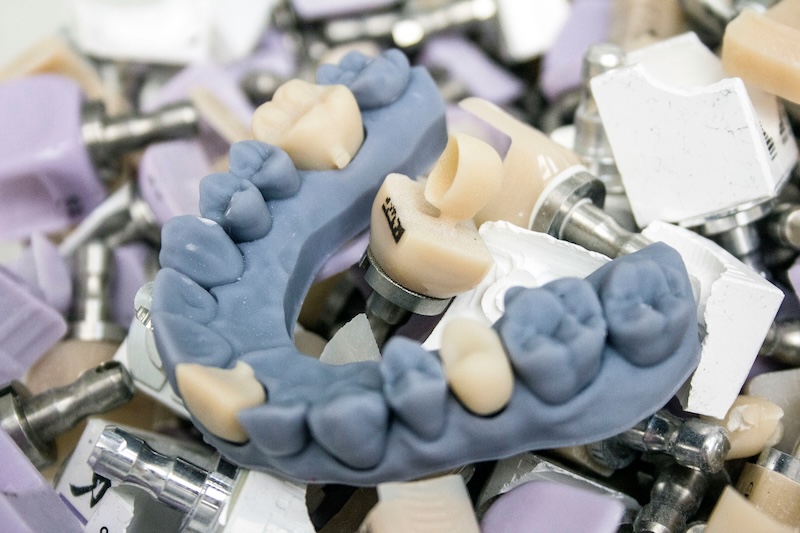
How Does Titanium’s Design Flexibility Enhance Innovation in Manufacturing?
3D printing with titanium supports the creation of complex, intricate designs that are difficult to achieve through traditional manufacturing. This flexibility has broadened the possibilities for innovation across industries.
Advantages in Manufacturing:
• Complex Geometries: Titanium powder can be used to create parts with complex internal structures that improve functionality and reduce weight.
• Customized Components: With titanium’s formability, I can design parts tailored to specific applications, maximizing performance and efficiency.
The design flexibility of titanium has enabled me to produce parts with intricate features and customized dimensions, transforming what’s possible in modern manufacturing.
Why Is Titanium’s Sustainability Important in 3D Printing?
Titanium’s high efficiency in additive manufacturing contributes to more sustainable production processes. Using only the material needed for each part reduces waste and promotes eco-friendly manufacturing.
Advantages for Sustainability:
• Minimal Material Waste: With 3D printing, only the necessary amount of titanium powder is used, significantly reducing waste.
• Reduced Carbon Footprint: By enabling lightweight, efficient designs, titanium 3D printing supports sustainability initiatives in various industries.
In my view, titanium’s efficiency in 3D printing aligns with a greener future, allowing me to produce high-quality components with a reduced environmental impact.
Claim: Why Titanium Is Transforming 3D Printing Across Industries
Titanium’s lightweight strength, biocompatibility, corrosion resistance, and design flexibility make it an invaluable material for 3D printing across diverse industries. These benefits enable manufacturers to produce innovative, durable, and highly efficient parts, driving advancements in aerospace, healthcare, automotive, and more.
Conclusion: How Titanium Is Shaping the Future of 3D Printing
Titanium’s unique properties have unlocked new possibilities in 3D printing, allowing for stronger, lighter, and more complex designs than ever before. Whether in aerospace, healthcare, automotive, or marine applications, titanium is setting a new standard in manufacturing with its adaptability and reliability.
For me, titanium’s integration into 3D printing has been transformative. It’s an ideal material for creating parts that need to be both robust and precise, pushing the limits of what modern manufacturing can achieve. As 3D printing continues to grow, titanium will remain a key player, shaping a future where innovation and quality go hand in hand.