Introduction
Titanium has become a popular material in 3D printing, especially in industries such as aerospace, medical, and automotive. Its unique properties, including a high strength-to-weight ratio, excellent corrosion resistance, and biocompatibility, make titanium an ideal material for additive manufacturing. Using titanium in 3D printing allows for the production of complex, lightweight components with high precision and minimal material waste.
In this article, we explore the various applications of titanium in 3D printing, highlighting its benefits and why it is a preferred material for advanced manufacturing technologies.
Features of Titanium
Titanium offers several key features that make it particularly suitable for 3D printing applications:
- High Strength-to-Weight Ratio: Titanium’s combination of strength and low weight makes it suitable for producing lightweight, yet strong components through 3D printing.
- Corrosion Resistance: Titanium’s resistance to corrosion ensures the longevity and durability of 3D-printed parts, even in harsh environments.
- Biocompatibility: Titanium is non-toxic and biocompatible, making it ideal for medical implants and devices created through 3D printing.
- Thermal Stability: Titanium can withstand high temperatures, making it suitable for applications that require resistance to heat.
The Most Commonly Used Grades of Titanium in 3D Printing
- Grade 5 Titanium (Ti-6Al-4V): Grade 5 titanium is an alloy that provides high strength, excellent corrosion resistance, and good weldability, making it the most commonly used grade in 3D printing.
- Grade 23 Titanium (Ti-6Al-4V ELI): Grade 23 titanium is an extra-low interstitial version of Grade 5, offering improved fracture toughness, making it suitable for medical implants that require additional durability.
Advantages of Titanium in 3D Printing
The use of titanium in 3D printing offers numerous advantages:
- Complex Geometries: Titanium’s compatibility with 3D printing allows for the creation of intricate and complex geometries that would be difficult or impossible to achieve with traditional manufacturing.
- Material Efficiency: 3D printing with titanium results in minimal material waste, making it a cost-effective solution for high-value applications.
- Customization: Titanium 3D printing enables the production of customized parts, particularly in the medical field where patient-specific implants are required.
- Reduced Lead Times: Additive manufacturing with titanium reduces lead times compared to traditional manufacturing processes, allowing for faster prototyping and production.
Key Applications of Titanium in 3D Printing
Titanium is used in a wide range of 3D printing applications, including:
- Aerospace Components: Titanium is used to 3D print lightweight and complex components for aircraft, such as brackets, ducts, and engine parts, where weight reduction is crucial for fuel efficiency.
- Medical Implants: Titanium’s biocompatibility makes it ideal for 3D-printed medical implants, including orthopedic implants and dental implants, which can be customized to fit individual patients.
- Automotive Parts: Titanium is used in 3D printing for high-performance automotive components, such as engine parts and exhaust systems, where strength and weight reduction are critical.
- Prosthetics: Titanium is used to create customized prosthetic limbs and components that are lightweight, durable, and tailored to the needs of individual patients.
- Tooling and Fixtures: Titanium is used to 3D print specialized tooling and fixtures that require high strength and durability, reducing the time and cost of production.
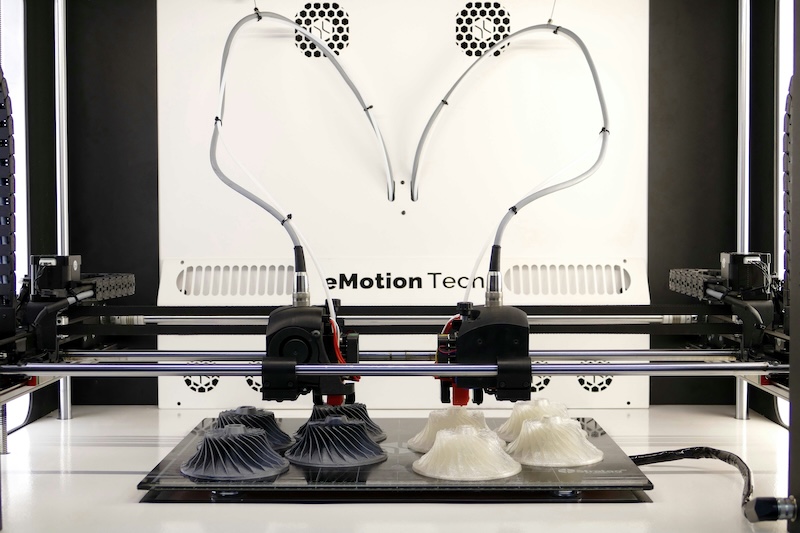
Comparisons: Titanium vs. Other Materials in 3D Printing
Titanium is often compared to other materials used in 3D printing, such as aluminum, stainless steel, and polymers:
- Titanium vs. Aluminum: Aluminum is commonly used in 3D printing due to its lightweight properties, but titanium offers superior strength and corrosion resistance, making it preferable for applications that require high strength.
- Titanium vs. Stainless Steel: Stainless steel is strong but significantly heavier than titanium. Titanium’s high strength-to-weight ratio makes it ideal for applications where weight reduction is critical.
- Titanium vs. Polymers: Polymers are used for 3D printing lightweight components, but titanium offers greater strength, durability, and heat resistance, making it suitable for demanding applications.
Benefits of Using Titanium in 3D Printing
The benefits of using titanium in 3D printing are numerous:
- Design Flexibility: 3D printing with titanium allows for complex and optimized designs that reduce weight while maintaining strength.
- Enhanced Performance: Titanium’s properties, combined with the precision of 3D printing, result in high-performance parts that are durable and reliable.
- Reduced Waste: Additive manufacturing with titanium reduces material waste compared to traditional subtractive methods, making it an environmentally friendly choice.
Challenges in Using Titanium in 3D Printing
Despite its advantages, there are challenges associated with using titanium in 3D printing:
- High Cost: Titanium powder used in 3D printing is more expensive compared to other materials, which can limit its use in cost-sensitive applications.
- Specialized Equipment: 3D printing with titanium requires specialized equipment and expertise, which can increase production costs.
- Post-Processing: Titanium parts often require post-processing, such as heat treatment or machining, to achieve the desired mechanical properties and surface finish.
Future Trends for Titanium in 3D Printing
The use of titanium in 3D printing is expected to grow as advancements in additive manufacturing technologies make it more accessible and cost-effective. Emerging trends include the development of more efficient titanium powder production methods and improvements in 3D printing techniques that reduce material waste and production costs. Titanium’s role in aerospace, medical, and automotive industries is likely to expand, with a focus on producing customized, high-performance components.
FAQs about Titanium in 3D Printing
- Why is titanium used in 3D printing?
- Titanium is used in 3D printing due to its high strength, corrosion resistance, and ability to create complex, lightweight components.
- What types of components can be 3D printed with titanium?
- Titanium is used to 3D print aerospace components, medical implants, automotive parts, prosthetics, and specialized tooling.
- How does titanium 3D printing benefit the aerospace industry?
- Titanium 3D printing allows for the production of lightweight and complex components, improving fuel efficiency and performance in aircraft.
- Is titanium suitable for medical implants created through 3D printing?
- Yes, titanium’s biocompatibility makes it ideal for 3D-printed medical implants, which can be customized to fit individual patients.
- What are the advantages of titanium over aluminum in 3D printing?
- Titanium offers superior strength and corrosion resistance compared to aluminum, making it preferable for high-stress applications.
- Can titanium be used to 3D print automotive parts?
- Yes, titanium is used to 3D print high-performance automotive components where strength and weight reduction are critical.
- What challenges are associated with 3D printing titanium?
- The main challenges include the high cost of titanium powder, the need for specialized equipment, and the requirement for post-processing.
- How does titanium 3D printing contribute to reduced waste?
- Additive manufacturing with titanium minimizes material waste compared to traditional subtractive methods, making it an environmentally friendly option.
- Why is titanium used in 3D-printed prosthetics?
- Titanium’s high strength-to-weight ratio and biocompatibility make it ideal for customized prosthetic limbs that are lightweight and durable.
- Is titanium used in 3D printing for tooling and fixtures?
- Yes, titanium is used to 3D print specialized tooling and fixtures that require high strength and durability.
- How does titanium compare to stainless steel in 3D printing?
- While stainless steel is strong, titanium offers comparable strength at a significantly lower weight, making it suitable for weight-sensitive applications.
- What future developments are expected for titanium in 3D printing?
- Advances in titanium powder production and 3D printing techniques are expected to make titanium more cost-effective and expand its use in various industries.
- Can titanium withstand high temperatures in 3D-printed applications?
- Yes, titanium’s thermal stability makes it suitable for components that need to withstand high temperatures.
- Why is titanium suitable for complex geometries in 3D printing?
- Titanium’s compatibility with 3D printing allows for the creation of intricate and complex geometries that would be challenging with traditional manufacturing.
- How does titanium contribute to the performance of 3D-printed aerospace components?
- Titanium’s lightweight properties and strength enhance the performance of aerospace components, improving fuel efficiency and reliability.
Conclusion
Titanium’s unique properties make it an ideal material for use in 3D printing. Its high strength-to-weight ratio, corrosion resistance, and biocompatibility make it invaluable for a wide range of applications, from aerospace and medical implants to automotive components and prosthetics. Despite challenges related to cost and specialized equipment, the benefits of using titanium in 3D printing far outweigh the drawbacks, ensuring its expanding role in the future of additive manufacturing.