Introduction: Titanium powder is revolutionizing personalized medicine.
Titanium, known for its strength, lightweight nature, and biocompatibility, has long been a preferred material for medical implants. However, with the rise of advanced manufacturing techniques like 3D printing, titanium powder is playing a pivotal role in enabling patient-specific medical solutions. By leveraging titanium powder, manufacturers can create highly customized implants and medical devices that are tailored to the unique needs of individual patients. But how exactly does titanium powder contribute to the development of these personalized medical solutions?
Titanium powder, through additive manufacturing, enables the creation of bespoke medical solutions, improving patient outcomes by offering precision, comfort, and faster recovery.
Let’s explore how titanium powder is transforming the field of patient-specific medical solutions, including its applications in implants, prosthetics, and surgical tools.
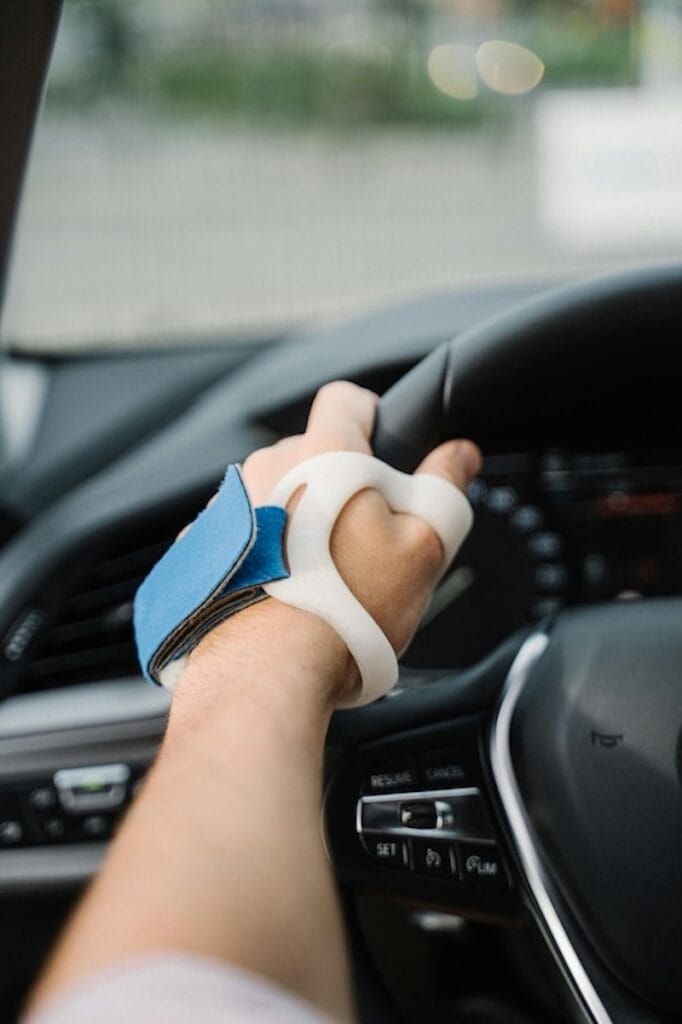
What Role Does Titanium Powder Play in Additive Manufacturing for Medical Solutions?
Additive manufacturing, often referred to as 3D printing, is the primary method through which titanium powder is used to create customized medical devices. This process involves building up layers of material to form a product, which is especially beneficial for creating patient-specific solutions.
• 3D Printing for Custom Implants: Titanium powder allows for the precise design and production of custom implants that perfectly match a patient’s anatomy. For instance, titanium powder is used to print custom joint replacements, such as hip or knee implants, that fit a patient’s unique bone structure, improving comfort and functionality.
• Faster Prototyping and Production: The ability to 3D print patient-specific titanium implants reduces the time required for prototyping and manufacturing compared to traditional methods. Surgeons and medical professionals can now order custom implants that are ready for use in a fraction of the time it once took.
Titanium powder enables 3D printing of highly personalized medical devices, drastically improving the speed and accuracy of custom implant production.
How Does Titanium Powder Enhance the Biocompatibility of Medical Implants?
One of the most crucial factors when designing medical implants is ensuring their compatibility with the human body. Titanium is known for its exceptional biocompatibility, making it an ideal material for implants that need to coexist with human tissue. By using titanium powder in additive manufacturing, several enhancements can be made:
• Porous Structures for Better Integration: Titanium powder can be used to create porous surfaces that mimic the structure of bone. This porosity encourages the natural growth of bone tissue into the implant, promoting better integration and reducing the risk of implant rejection.
• Customizable Surface Treatment: The powder form allows for greater control over the surface properties of the implant. For instance, the surface of titanium implants made from powder can be treated to enhance osseointegration, improving the bond between the implant and bone tissue.
Titanium powder offers biocompatible implants with customizable features like porosity, enhancing the integration between the implant and natural tissue.
How Does Titanium Powder Support Personalized Prosthetics?
In addition to implants, titanium powder is also used to manufacture highly personalized prosthetics. Prosthetics, whether for limbs or facial reconstruction, require a high level of customization to match the patient’s anatomy. Titanium powder is especially beneficial in these applications due to its properties:
• Lightweight Yet Strong Prosthetics: Prosthetic limbs made from titanium are lighter and stronger than those made from traditional metals. The use of titanium powder in 3D printing enables the creation of customized prosthetic components that are both durable and lightweight, improving the comfort and functionality for patients.
• Custom Fit and Design: Titanium powder allows for intricate designs, creating prosthetics that are tailored precisely to the patient’s needs. For example, a patient needing a custom limb can have a prosthesis that perfectly matches their body shape, ensuring better fit, mobility, and overall user satisfaction.
Titanium powder is key to producing lightweight, strong, and highly personalized prosthetic solutions, improving mobility and quality of life for patients.
How Does Titanium Powder Improve the Functionality of Surgical Instruments?
Surgical tools, particularly those used in delicate procedures, must be precisely engineered for performance. Titanium powder is making it possible to design surgical instruments that are not only high-performing but also patient-specific:
• Customized Surgical Tools: Surgeons can now order custom titanium surgical tools made specifically for the requirements of a procedure, ensuring better precision and efficiency. This is particularly useful for complex surgeries that require highly specialized instruments.
• Biocompatibility in Tools: Titanium’s biocompatibility extends to surgical tools as well. Instruments made from titanium powder can be engineered to reduce the risk of tissue irritation or allergic reactions during surgery.
Titanium powder allows for the production of highly specialized and biocompatible surgical instruments that improve the precision and outcomes of medical procedures.
How Does Titanium Powder Enable Faster Recovery and Better Outcomes for Patients?
The customization made possible by titanium powder not only improves the fit of implants but also has a direct impact on recovery time and long-term health outcomes:
• Better Fit, Less Stress: Customized implants that fit better reduce the stress on surrounding tissues, minimizing discomfort and pain during recovery. For example, a custom hip implant made from titanium powder is likely to fit better and cause less wear and tear on the surrounding bone and tissue, which in turn reduces the chance of complications.
• Faster Healing: Implants designed with optimal fit and biocompatibility encourage faster healing and quicker recovery. Patients with customized implants made from titanium powder often experience less inflammation and reduced risk of infection.
The precision and fit of implants made from titanium powder reduce recovery times and enhance long-term outcomes for patients.
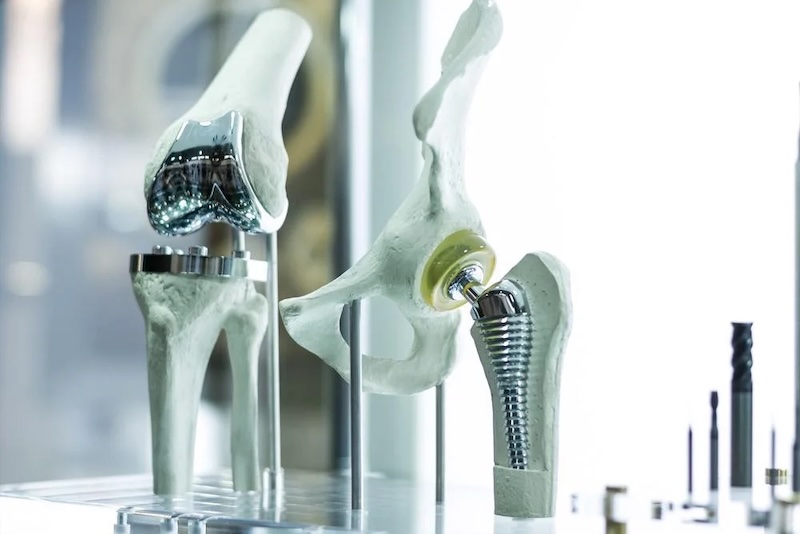
How Does Titanium Powder Contribute to the Sustainability of Medical Devices?
Sustainability is increasingly becoming a key concern in the medical field. Titanium powder, due to its unique properties, can contribute to more sustainable medical solutions in several ways:
• Minimal Material Waste: Additive manufacturing using titanium powder produces far less material waste compared to traditional subtractive manufacturing processes. This reduces the environmental impact associated with material loss and the need for recycling.
• Longer-Lasting Implants: Titanium is known for its longevity, and implants made from titanium powder can offer improved durability. This extends the life of medical implants, reducing the need for frequent replacements and minimizing waste.
Titanium powder supports sustainability by reducing material waste and increasing the longevity of medical devices.
Claim: Titanium Powder is Transforming Personalized Medical Solutions
Titanium powder plays an essential role in revolutionizing the field of personalized medicine by enabling the production of highly customized, biocompatible implants, prosthetics, and surgical tools. With the advancements in 3D printing, the medical field can now provide more accurate, tailored solutions that improve patient outcomes, reduce recovery time, and promote long-term health benefits.
Conclusion: Titanium Powder Is a Game-Changer for Patient-Specific Medical Solutions
As someone deeply involved in the field, I believe that titanium powder is a key enabler of the future of personalized medicine. Its versatility in additive manufacturing opens up a new realm of possibilities for medical solutions that are specifically tailored to the needs of individual patients. With improved biocompatibility, faster recovery times, and more sustainable practices, titanium powder is shaping the future of medical device design and patient care, and I’m excited to see how it continues to evolve.
One Response