Introduction: The Impact of Titanium Powder on Advanced Manufacturing
In the world of modern manufacturing, materials with unique properties drive innovation. Titanium powder has become a breakthrough in industries that rely on high-performance, lightweight, and durable materials. As a cornerstone of additive manufacturing, titanium powder is transforming everything from aerospace components to medical implants. But how exactly is titanium powder shaping the future of manufacturing?
Titanium powder offers exceptional strength, lightweight characteristics, and adaptability for complex designs, enabling precision manufacturing for industries like aerospace, healthcare, and automotive. This innovative material supports intricate design, waste reduction, and efficiency, marking a significant advancement in manufacturing technology.
Below, let’s explore the key benefits, applications, and transformative impact of titanium powder on modern manufacturing.
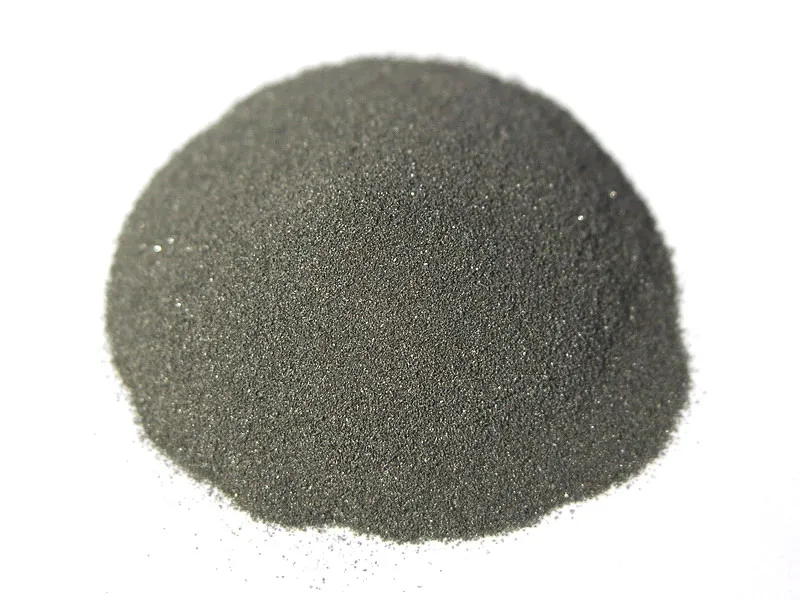
What Makes Titanium Powder Ideal for Additive Manufacturing?
Titanium powder is uniquely suited for additive manufacturing (3D printing) due to its particle consistency, strength, and ability to form complex shapes layer by layer. This capability has led to breakthroughs in customized manufacturing and complex geometries.
Advantages in Additive Manufacturing:
• Precision and Customization: Titanium powder allows for highly detailed and customized designs that would be impossible with traditional methods.
• Reduced Material Waste: Additive manufacturing with titanium powder minimizes waste by using only the exact amount of material needed for each part.
From my perspective, titanium powder is invaluable for intricate designs, allowing me to create components with precision and customization that surpass traditional limitations.
How Does Titanium Powder Contribute to Lightweight, High-Strength Components?
The high strength-to-weight ratio of titanium powder makes it a top choice for components that need to be strong but lightweight, especially in aerospace and automotive industries.
Advantages of Lightweight Strength:
• Enhanced Performance: In aerospace and automotive applications, titanium’s lightweight yet strong properties improve fuel efficiency and performance.
• Reduced Structural Weight: Titanium powder allows for lighter designs without sacrificing structural integrity, which is crucial for high-stakes applications.
With titanium powder, I can produce components that are both strong and light, making them ideal for uses where every gram counts, like in aircraft and high-performance vehicles.

Why Is Titanium Powder So Effective for Medical Applications?
Titanium powder’s biocompatibility makes it especially useful in medical applications. Additive manufacturing with titanium powder allows for customized, patient-specific implants and devices that integrate seamlessly with the body.
Advantages in Medical Applications:
• Biocompatibility for Implants: Titanium powder can be used to create implants that won’t cause adverse reactions, reducing risks for patients.
• Customization and Fit: With 3D printing, I can produce medical implants tailored to individual patients’ anatomies, improving comfort and functionality.
In healthcare, titanium powder’s adaptability and safety have redefined the possibilities for creating patient-specific solutions, enhancing both outcomes and patient comfort.
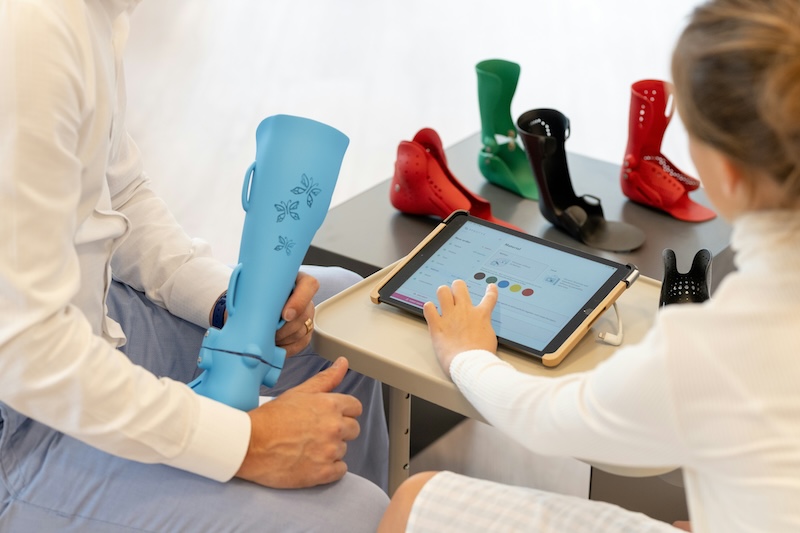
How Does Titanium Powder Improve Design Flexibility in Manufacturing?
Titanium powder supports complex geometries and intricate designs that traditional manufacturing methods struggle to achieve. This flexibility has expanded possibilities for innovation across industries.
Advantages in Design Flexibility:
• Complex Geometries: Titanium powder can be used to create parts with intricate internal structures that were previously impossible to manufacture.
• Enhanced Product Functionality: Design freedom allows me to incorporate functional enhancements directly into a part, optimizing performance and functionality.
The design flexibility of titanium powder has enabled me to create parts with features that would be challenging or costly to produce with conventional techniques, allowing for more innovative product designs.
How Does Titanium Powder Support Sustainability in Manufacturing?
Using titanium powder in additive manufacturing reduces waste and energy usage, making it a more sustainable option. This reduction is beneficial for industries that seek to lower their environmental impact.
Advantages for Sustainability:
• Minimal Material Waste: Additive manufacturing only uses the necessary amount of titanium powder, significantly reducing waste compared to traditional methods.
• Lower Carbon Footprint: Producing parts layer by layer requires less energy, aligning with green manufacturing initiatives.
By adopting titanium powder in my processes, I’ve seen a reduction in waste and a more efficient production approach, which contributes to sustainability goals and cost savings.
Why Is Titanium Powder Important for High-Temperature Applications?
Titanium powder’s thermal stability makes it suitable for high-temperature applications where components must retain their strength and form. This is critical in industries like aerospace and energy.
Advantages in High-Temperature Applications:
• Resistant to Heat Deformation: Titanium powder retains its properties under high temperatures, ideal for engines, turbines, and other heat-intensive applications.
• Improved Durability in Extreme Conditions: Components made from titanium powder are more durable and resistant to thermal stress.
Using titanium powder in high-temperature settings ensures that parts perform consistently, even in challenging environments where other materials might fail.
How Is Titanium Powder Contributing to Cost Efficiency in Production?
Though titanium itself can be expensive, titanium powder used in additive manufacturing can be more cost-effective by reducing material waste and enabling faster production cycles.
Advantages of Cost Efficiency:
• Material Savings: Additive manufacturing uses only the necessary amount of titanium powder, cutting down on waste and associated costs.
• Faster Production: Producing parts directly from digital designs saves time and reduces labor costs compared to traditional machining.
In my experience, using titanium powder helps streamline the production process and control costs, making high-quality titanium components more accessible.
Claim: Why Titanium Powder Is Revolutionizing Modern Manufacturing
Titanium powder’s adaptability, strength, lightweight characteristics, biocompatibility, and sustainability make it an ideal material for various advanced manufacturing needs. These benefits have helped redefine how components are designed, produced, and applied across multiple sectors.
Conclusion: How Titanium Powder Is Shaping the Future of Manufacturing
Titanium powder is a transformative material, providing solutions that meet the demands of modern manufacturing. Its versatility, coupled with strength and sustainability, is paving the way for more innovative, efficient, and eco-friendly production methods.
For manufacturers like myself, titanium powder offers a path forward for creating reliable, high-performance components in industries from aerospace to healthcare. It’s an investment in a future where precision, strength, and sustainability come together to create better products and meet the demands of an evolving world.