Introduction: The Role of Alloying in Titanium Forgings
Titanium’s natural properties, such as its high strength-to-weight ratio, corrosion resistance, and biocompatibility, make it a sought-after material in many industries. However, adding alloying elements to titanium can enhance its performance further, tailoring it for specific applications. But how exactly do these alloying elements improve the properties of titanium forgings?
The addition of alloying elements to titanium enhances its strength, ductility, heat resistance, and corrosion protection, making titanium forgings versatile for critical and high-performance applications.
Let me explain how different alloying elements work to elevate titanium’s capabilities in various industries.
How Do Alloying Elements Increase Strength?
Alloying elements, such as aluminum and vanadium, are commonly added to titanium to enhance its mechanical strength.
Key benefits:
• Solid Solution Strengthening: Elements like aluminum increase the base strength of the titanium matrix.
• Beta-Phase Stabilization: Vanadium stabilizes the beta phase, improving flexibility and strength during heat treatment.
• Microstructural Refinement: The addition of alloying elements promotes finer grain structures, which contribute to greater overall strength.
For me, the ability to tailor titanium’s strength through alloying is critical for applications requiring exceptional load-bearing capacity, such as aerospace components.
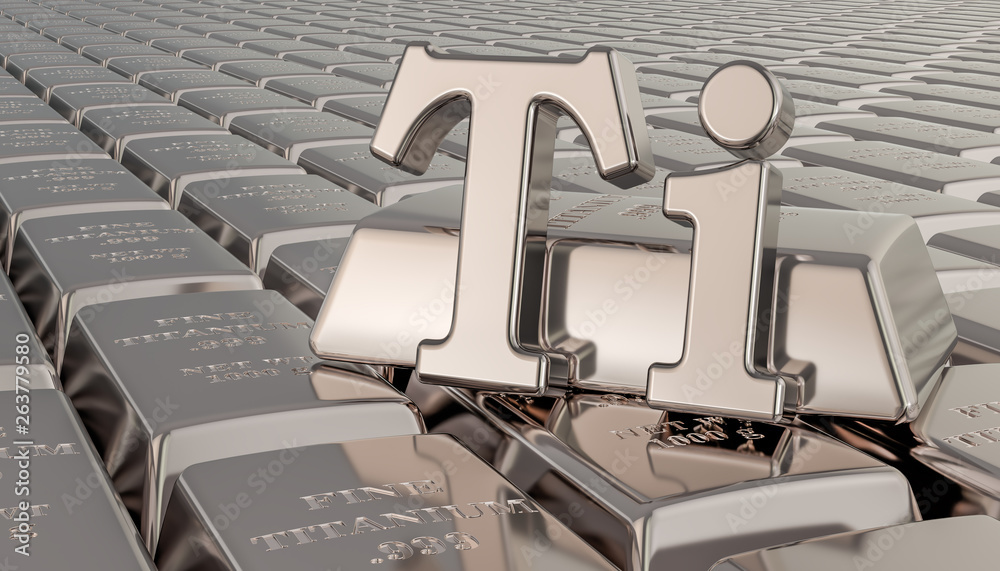
How Do Alloying Elements Improve Corrosion Resistance?
Titanium is naturally corrosion-resistant, but alloying elements can further enhance this property for harsh environments.
Key points:
• Molybdenum: Improves resistance to pitting and crevice corrosion, making it ideal for marine and chemical processing applications.
• Nickel: Enhances performance in highly corrosive environments, such as offshore energy systems.
• Palladium: Boosts resistance to acid corrosion, especially in chloride-rich environments.
Alloying titanium for corrosion resistance ensures its durability and reliability in extreme conditions, from subsea to industrial applications.
How Does Alloying Enhance Heat Resistance?
High-temperature applications, such as jet engines and turbines, demand materials that retain their strength and stability under extreme heat. Alloying elements enable titanium to meet these requirements.
Key contributions:
• Aluminum: Stabilizes the alpha phase, improving performance at elevated temperatures.
• Zirconium: Enhances creep resistance, preventing deformation under prolonged high-temperature stress.
• Tin: Improves oxidation resistance, protecting components in high-heat environments.
Alloying titanium for heat resistance is essential for ensuring safety and efficiency in aerospace and energy systems.
How Do Alloying Elements Affect Ductility and Formability?
While titanium is inherently strong, alloying can improve its ductility and ease of manufacturing.
Key improvements:
• Vanadium and Manganese: Increase formability without compromising strength, making titanium easier to shape during forging.
• Beta Alloys: Adding elements like molybdenum results in beta-phase titanium, which offers higher ductility for complex designs.
For me, these enhancements allow titanium forgings to meet the demands of intricate applications, such as medical implants and automotive parts.
How Do Alloying Elements Influence Fatigue Resistance?
Fatigue resistance is critical for components subjected to repeated stress cycles. Alloying elements enhance this property in titanium.
Key benefits:
• Chromium and Zirconium: Increase resistance to crack initiation and propagation under cyclic loads.
• Nickel: Enhances the toughness and fatigue strength of titanium alloys, ensuring longevity in dynamic environments.
These improvements make titanium forgings indispensable for fatigue-critical applications like suspension systems and marine structures.
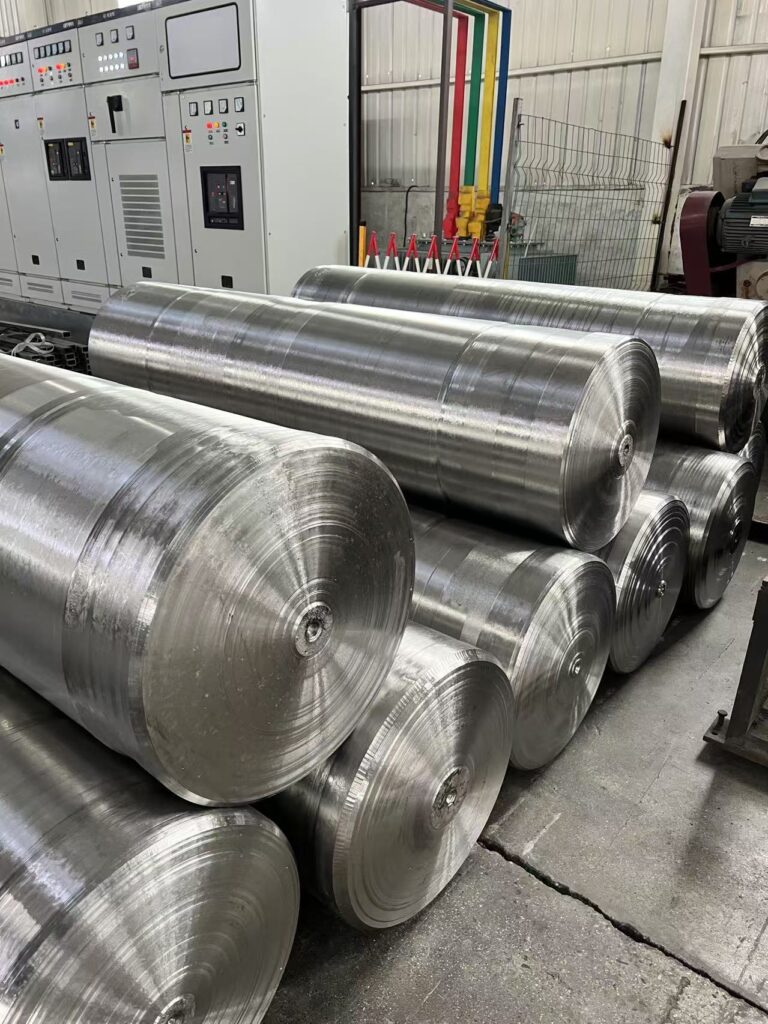
How Are Titanium Alloys Tailored for Specific Industries?
Alloying elements allow titanium to be customized for industry-specific needs, expanding its range of applications.
Examples include:
• Aerospace: Ti-6Al-4V (Grade 5) combines aluminum and vanadium for high strength, fatigue resistance, and heat stability.
• Medical: Ti-6Al-4V ELI (Grade 23) includes extra low interstitials for improved biocompatibility and ductility.
• Energy: Beta alloys, with molybdenum and chromium, offer enhanced durability in high-pressure and corrosive environments.
This versatility demonstrates how alloying elements transform titanium into a material suited for the most demanding applications.
Claim: Why Alloying Elements Are Essential for Titanium Forgings
The addition of alloying elements enhances titanium forgings by improving strength, corrosion resistance, heat stability, ductility, and fatigue resistance. This tailoring ensures that titanium meets the specialized demands of various industries.
Conclusion: Unlocking Titanium’s Full Potential Through Alloying
When I consider the role of alloying elements in titanium forgings, I see a material that’s been transformed into a versatile powerhouse. These enhancements allow titanium to excel in critical applications, from aerospace to energy. For me, the art and science of alloying titanium are what truly unlock its full potential, enabling it to meet the evolving challenges of modern engineering.