Introduction: Advanced automation is transforming the manufacturing of triply circles.
The production of triply circles, essential components in cookware, has benefited greatly from advancements in automated equipment. Automation in manufacturing ensures higher precision, faster production rates, and cost efficiency. But how does this advanced automated technology specifically improve the production process of triply circles?
Automation in triply circle production enhances efficiency, precision, and quality control, allowing manufacturers to meet growing demands with consistency.
Let’s explore the ways in which advanced automated equipment contributes to the development of high-quality triply circles.
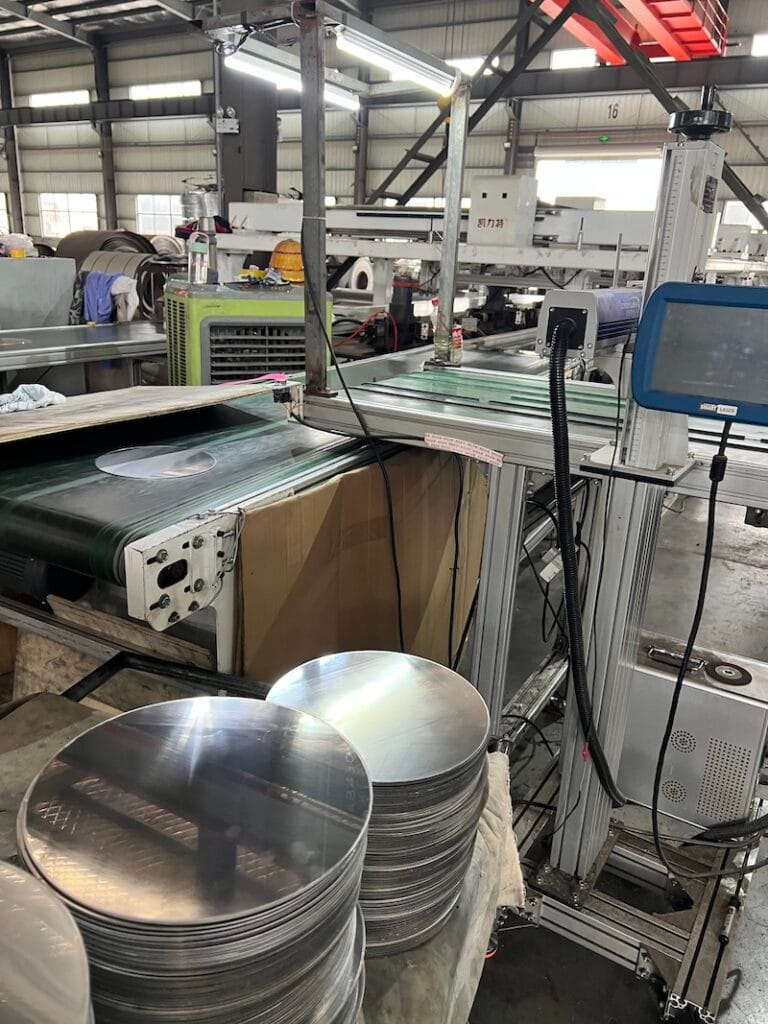
How Does Automation Enhance the Precision of Triply Circle Manufacturing?
Precision is crucial in the production of triply circles, as even minor variations in thickness or alignment can affect cooking performance. Automated systems are designed to maintain strict tolerances, ensuring that each triply circle is manufactured to exact specifications.
• Automated Cutting and Shaping: Advanced machinery can cut, stamp, and shape the base materials of the triply circles with minimal human intervention, providing consistent results across large volumes of production. Automated processes can precisely cut the materials to the exact diameter and thickness required, ensuring that every piece meets the same standards.
• Laser Measurement Technology: Modern automated equipment integrates laser measurement and scanning technologies to measure the thickness, diameter, and quality of the triply circles in real time. This allows manufacturers to detect and correct defects immediately, maintaining high levels of precision throughout the production process.
Automation ensures that triply circles are produced with high precision, resulting in better cooking performance and more uniform products.
How Does Automation Improve Production Speed and Efficiency?
One of the major benefits of advanced automated equipment in manufacturing is the significant boost in production speed and overall efficiency.
• Faster Production Cycles: Automated systems can work at faster speeds than manual labor, allowing manufacturers to produce larger quantities of triply circles in shorter timeframes. This increased throughput helps meet the high demand for cookware components, especially in global markets.
• Continuous Production: Automation enables continuous production, reducing downtime. Machines can operate around the clock, with minimal interruptions, ensuring consistent output without the fatigue or errors associated with manual labor. This also optimizes energy usage and reduces operational costs.
Automated equipment boosts production speed and efficiency, allowing manufacturers to scale production without sacrificing quality.
How Does Automation Enhance Quality Control in Triply Circle Production?
Ensuring the quality of each triply circle is vital to its functionality and durability. Automation plays a key role in maintaining quality control across every step of the manufacturing process.
• Real-Time Quality Monitoring: Automated systems often include built-in sensors and cameras that continuously monitor the production process. These tools can detect imperfections, such as surface defects, misalignments, or irregular thickness, before the product moves further down the production line. This instant feedback loop ensures that quality is maintained throughout the process.
• Reduced Human Error: By minimizing the need for manual intervention, automation reduces the risk of errors, ensuring that each triply circle is produced to the highest standards. Automated equipment also performs repetitive tasks with greater consistency than human workers, ensuring uniformity in product quality.
Automation provides consistent quality control, ensuring each triply circle meets the necessary standards for performance and durability.
How Does Automation Reduce Material Waste in Triply Circle Manufacturing?
Material waste can be a significant cost in manufacturing, especially when working with high-quality materials like stainless steel, aluminum, and titanium in triply circle production. Automation helps reduce waste by optimizing the use of materials throughout the manufacturing process.
• Precise Material Usage: Automated cutting and stamping equipment can cut materials with extreme accuracy, minimizing scrap and ensuring that each piece of raw material is utilized efficiently. This reduces the amount of excess material that needs to be discarded, lowering production costs and contributing to sustainability.
• Optimized Material Yield: Advanced software used in automated systems can calculate the best way to utilize the available raw materials, improving material yield and reducing overall waste. This results in better cost management and a more eco-friendly manufacturing process.
Automation improves material efficiency, reducing waste and making the production of triply circles more cost-effective and sustainable.
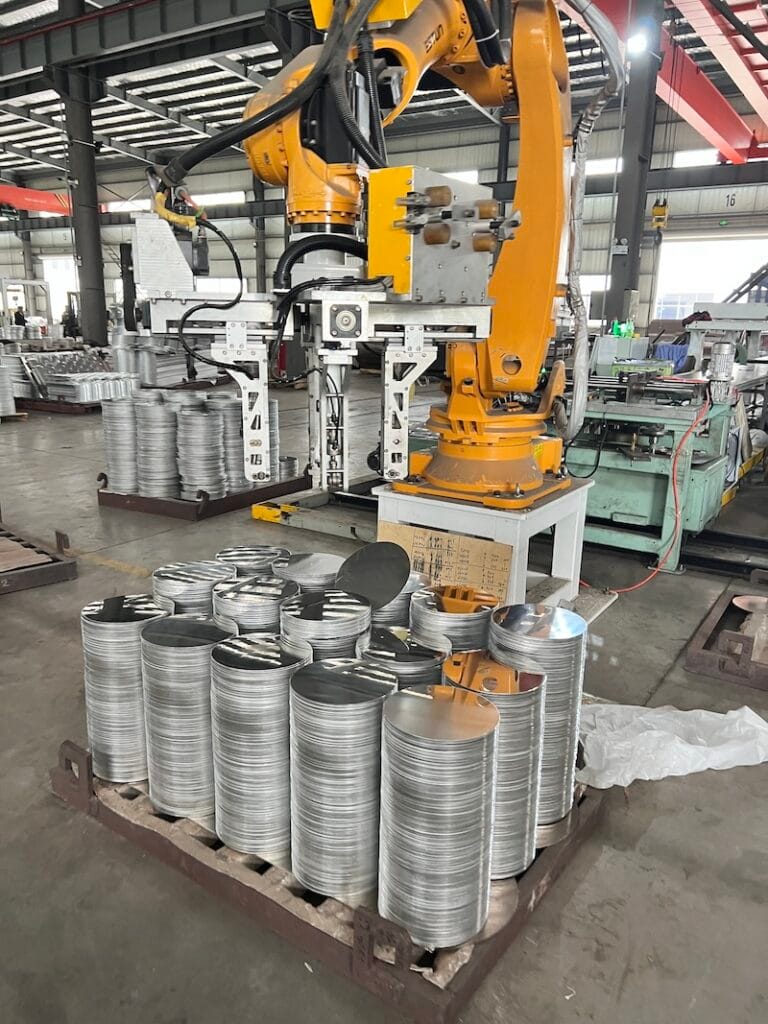
How Does Automation Improve Safety in Triply Circle Manufacturing?
Safety is a top priority in manufacturing, especially when working with metals that are heated or require heavy machinery. Automated equipment plays a significant role in enhancing safety within the production process.
• Reduced Human Exposure to Hazards: Automated machinery can handle dangerous tasks such as cutting, shaping, or handling hot materials, reducing the risk of injury to workers. This leads to a safer working environment and lowers the likelihood of accidents caused by human error.
• Automated Safety Features: Many modern automated systems are equipped with safety sensors, emergency stop mechanisms, and protective shields that automatically activate when a problem is detected. These safety features further protect workers and ensure smooth, uninterrupted production.
Automation enhances workplace safety by minimizing the need for manual handling of dangerous tasks and incorporating advanced safety systems.
How Does Automation Support Customization in Triply Circle Production?
Customization is becoming increasingly important in the cookware industry, where different markets demand varying specifications. Automation enables manufacturers to respond more flexibly to custom orders and adapt to changing consumer preferences.
• Flexible Manufacturing Systems: Automated systems can be reprogrammed to produce triply circles with different specifications, such as varying diameters, thicknesses, or materials. This flexibility allows manufacturers to accommodate custom orders and create specialized cookware components with minimal lead time.
• On-Demand Production: Automation supports on-demand production, where manufacturers can quickly adapt to fluctuations in customer demand for specific sizes, materials, or features. This helps manufacturers respond more efficiently to market changes and meet specific customer needs.
Automation enables flexible production, allowing manufacturers to meet customized orders and stay responsive to market trends.
Claim: Advanced Automated Equipment is Key to Efficient Triply Circle Production
The integration of advanced automated equipment in triply circle production has a transformative impact, enhancing precision, speed, efficiency, and safety. With automation, manufacturers can produce high-quality cookware components more consistently, at a lower cost, and with reduced environmental impact.
Conclusion: The Future of Triply Circle Manufacturing is Automated
In my view, the adoption of advanced automation is key to the continued success and growth of triply circle production. By increasing precision, improving material efficiency, enhancing quality control, and reducing human error, automation is helping manufacturers deliver high-performance cookware components at scale. As demand for triply cookware continues to rise, the role of automation will only become more critical in ensuring that production remains fast, efficient, and of the highest quality.