Introduction: The Demands of Extreme Pressure Environments
Applications such as subsea exploration, aerospace propulsion, and high-performance manufacturing often operate under extreme pressure conditions. Materials in these environments must exhibit exceptional strength, resilience, and reliability. Titanium forgings are widely recognized for their ability to withstand such demanding conditions. But what specific characteristics enable them to perform so effectively under extreme pressure?
Titanium forgings excel under extreme pressure due to their high strength-to-weight ratio, fatigue resistance, and ability to maintain structural integrity, making them indispensable in critical applications.
Let me explain why titanium forgings are the go-to solution for high-pressure challenges.
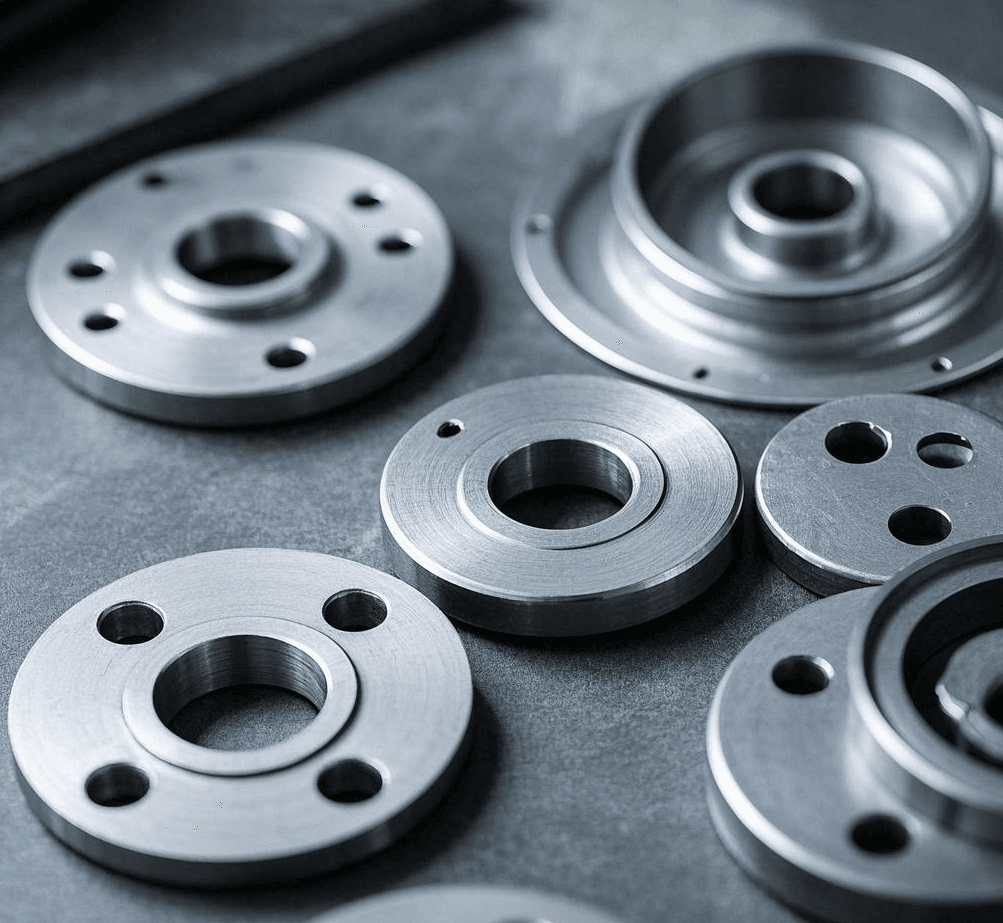
Why Is Titanium’s Strength-to-Weight Ratio Important for High Pressure?
Titanium’s superior strength-to-weight ratio allows it to endure extreme pressure without adding unnecessary bulk, making it ideal for weight-sensitive applications.
Key benefits:
• Reduced Structural Stress: The material’s strength ensures minimal deformation under pressure.
• Enhanced Efficiency: Lightweight components reduce energy consumption in systems like submarines or spacecraft.
• Optimal Performance: Titanium forgings handle pressure effectively without sacrificing weight-critical performance.
This property makes titanium forgings a standout choice for high-pressure applications in aerospace and marine engineering.
How Does Titanium’s Fatigue Resistance Enhance Its Performance?
Repeated pressure cycling can weaken materials over time, leading to fatigue failure. Titanium forgings offer exceptional resistance to this stress.
Key points:
• Crack Resistance: Forged titanium components resist the initiation and propagation of cracks under cyclic loads.
• Extended Lifespan: Fatigue resistance ensures durability in dynamic pressure environments like subsea equipment.
Resistance is vital for ensuring safety and reliability in critical systems operating under fluctuating pressures.
How Does Titanium Perform Against Creep Deformation?
Creep occurs when a material deforms over time under constant stress, particularly at elevated temperatures. Titanium forgings demonstrate excellent creep resistance.
Key advantages:
• Structural Integrity: Titanium maintains its shape and strength even under prolonged high-pressure conditions.
• Thermal Stability: Forgings perform well in applications combining high pressure and temperature, such as jet engines or power plants.
Titanium’s ability to resist creep ensures consistent performance in the harshest environments.
How Does Titanium Resist Corrosion in High-Pressure Environments?
High-pressure environments, especially subsea, are often corrosive, which can compromise the performance of many materials. Titanium’s natural corrosion resistance provides a critical advantage.
Key benefits:
• No Structural Degradation: Titanium’s oxide layer prevents material breakdown under pressure.
• Longevity in Saltwater: Titanium forgings remain durable even in deep-sea conditions, where pressure and salinity are extreme.
Corrosion resistance ensures the reliability of titanium components in offshore energy and marine exploration.
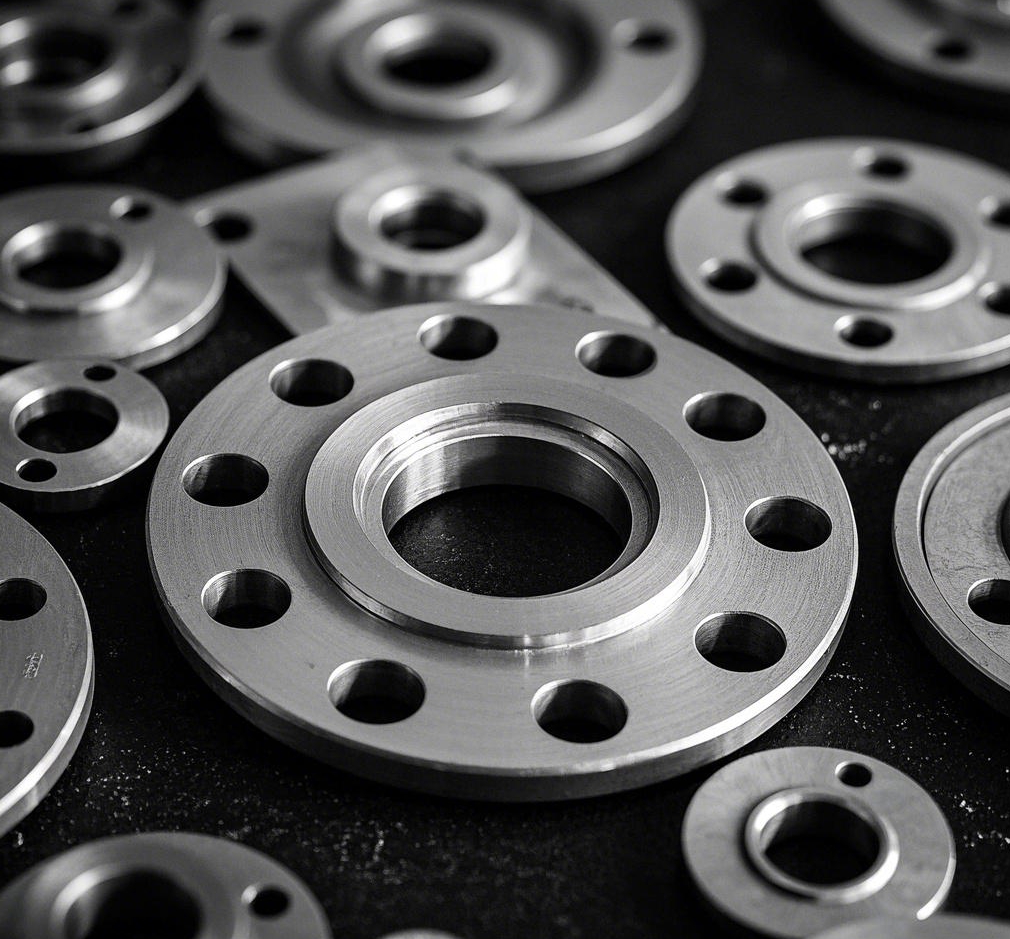
How Are Titanium Forgings Used in High-Pressure Applications?
Titanium forgings are employed in a variety of industries where high-pressure performance is essential.
Key applications include:
• Subsea Exploration: Forgings are used in pressure-resistant casings, valves, and risers.
• Aerospace Systems: Titanium components withstand high pressures in jet engines and fuel systems.
• Industrial Equipment: Forgings are critical in hydraulic systems and pressure vessels used in manufacturing and energy production.
These applications highlight titanium’s versatility and importance in modern engineering.
How Do Manufacturing Advances Improve Titanium’s Performance Under Pressure?
Advancements in forging techniques enhance titanium’s ability to withstand extreme pressure.
Key innovations:
• Isothermal Forging: Maintains uniform material properties, improving pressure resistance.
• Precision Forging: Reduces weak points by creating components with optimized grain structures.
• Hybrid Manufacturing: Combines forging with additive manufacturing to produce parts tailored for high-pressure environments.
These technological strides ensure titanium forgings continue to meet and exceed the demands of extreme applications.
Claim: Why Titanium Forgings Are Ideal for High-Pressure Conditions
Titanium forgings excel under extreme pressure due to their strength-to-weight ratio, fatigue resistance, corrosion resistance, and structural integrity. These qualities make them indispensable for applications in aerospace, marine, and industrial sectors.
Conclusion: Forged for Pressure Challenges
As I consider the capabilities of titanium forgings, their performance under extreme pressure stands out as one of their defining strengths. They represent the pinnacle of material science, combining resilience, durability, and adaptability. For me, titanium forgings are more than just a material—they are the key to unlocking possibilities in some of the world’s most demanding environments. With ongoing innovation, their role in high-pressure applications will only continue to expand, shaping the future of engineering and exploration.