Introduction: Advanced techniques are transforming titanium ingot manufacturing.
Titanium, known for its strength, lightweight nature, and corrosion resistance, has become a staple material in various industries, including aerospace, medical, automotive, and energy. However, the processing of titanium ingots has historically been challenging due to the material’s high melting point and reactivity. Recent advancements in processing techniques, such as vacuum arc remelting (VAR), electron beam melting (EBM), and isothermal forging, have revolutionized the way titanium ingots are produced and utilized in manufacturing. So how are these advancements impacting their use?
Advancements in processing techniques improve the quality, efficiency, and versatility of titanium ingots, enabling their use in high-performance and precision applications.
Let’s explore how these innovations are driving the adoption of titanium ingots across industries.
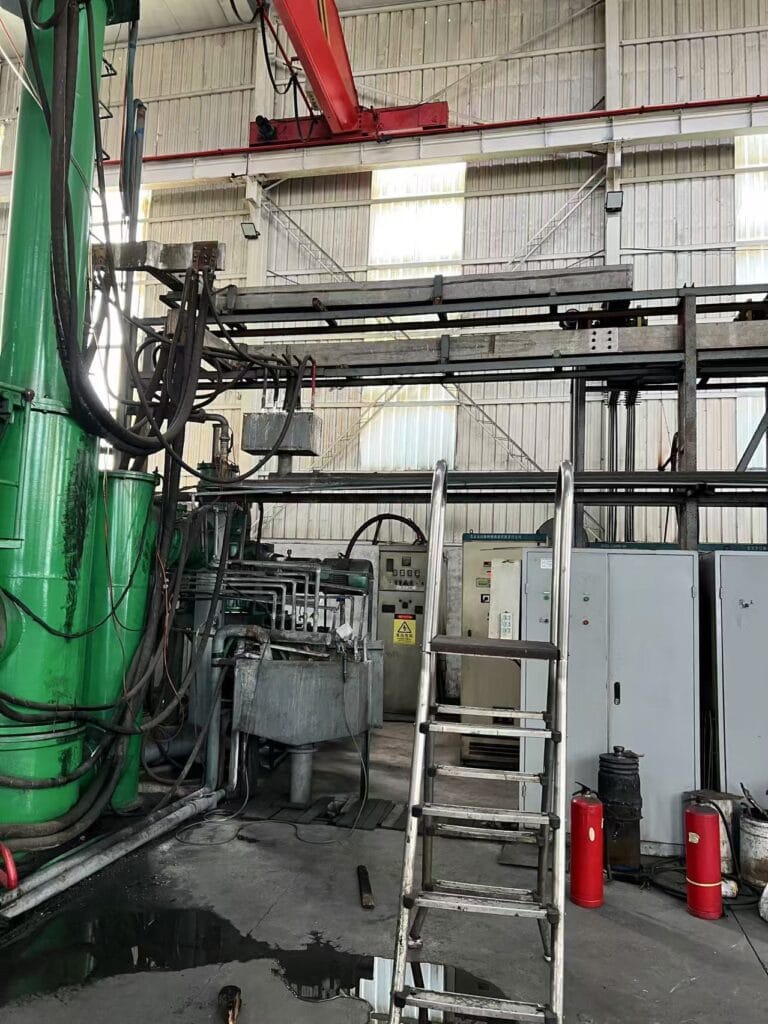
How Do Advanced Melting Techniques Improve Titanium Ingot Quality?
Modern melting techniques such as vacuum arc remelting (VAR) and electron beam melting (EBM) play a crucial role in producing high-quality titanium ingots.
• Vacuum Arc Remelting (VAR): This method involves melting titanium ingots in a vacuum environment to eliminate impurities such as oxygen, nitrogen, and carbon. The result is a homogenous ingot with fewer defects, ensuring better mechanical properties. VAR is especially critical for industries like aerospace, where high-quality materials are essential for safety and performance.
• Electron Beam Melting (EBM): EBM is used to melt titanium under high vacuum conditions, which prevents contamination and improves the purity of the final ingot. It allows for precise control over the ingot’s chemical composition and microstructure, resulting in improved strength and reliability.
These advanced melting techniques ensure titanium ingots are of high purity and uniform quality, essential for critical applications in aerospace and medical manufacturing.
How Does Isothermal Forging Enhance the Usability of Titanium Ingots?
Isothermal forging is another innovative process that significantly impacts the way titanium ingots are transformed into usable components.
• Uniform Deformation: By maintaining a constant temperature during the forging process, isothermal forging ensures that titanium retains its ductility, allowing for uniform deformation. This minimizes the risk of defects, such as cracking or warping, in the final product.
• Complex Shapes: This technique enables the production of intricate and high-precision components, such as jet engine blades and medical implants. The ability to forge titanium into complex shapes expands its applications in industries that demand detailed designs.
Isothermal forging improves the workability of titanium ingots, allowing for the creation of highly detailed and durable components.
How Are Additive Manufacturing Techniques Leveraging Titanium Ingots?
Additive manufacturing, or 3D printing, is another area where titanium ingots are finding new applications thanks to advancements in powder production techniques.
• Powder Production from Ingots: Titanium ingots are increasingly used to produce titanium powder, the raw material for 3D printing. Atomization processes convert ingots into fine, uniform powders that can be used in additive manufacturing to create custom, lightweight, and strong components.
• Customized Solutions: 3D printing allows manufacturers to create highly customized components with intricate geometries, such as medical implants and aerospace parts. The versatility of titanium powder derived from ingots has revolutionized production in these sectors.
By enabling the production of titanium powder, advancements in processing techniques are expanding the applications of titanium ingots in additive manufacturing.
How Do These Techniques Improve Cost Efficiency in Titanium Manufacturing?
Titanium has traditionally been expensive to process due to its high melting point and reactivity. Advancements in processing techniques are making titanium ingots more cost-efficient for manufacturers.
• Reduced Waste: Processes like VAR and isothermal forging minimize material waste by ensuring uniformity and reducing defects. This lowers the cost of rework and scrap, making titanium more economical to use.
• Energy Efficiency: Modern techniques such as plasma arc melting and electron beam melting consume less energy compared to older methods, reducing operational costs. This is particularly important in industries like automotive and energy, where cost efficiency is a priority.
Improved efficiency and reduced waste make titanium ingots more accessible for broader manufacturing applications.
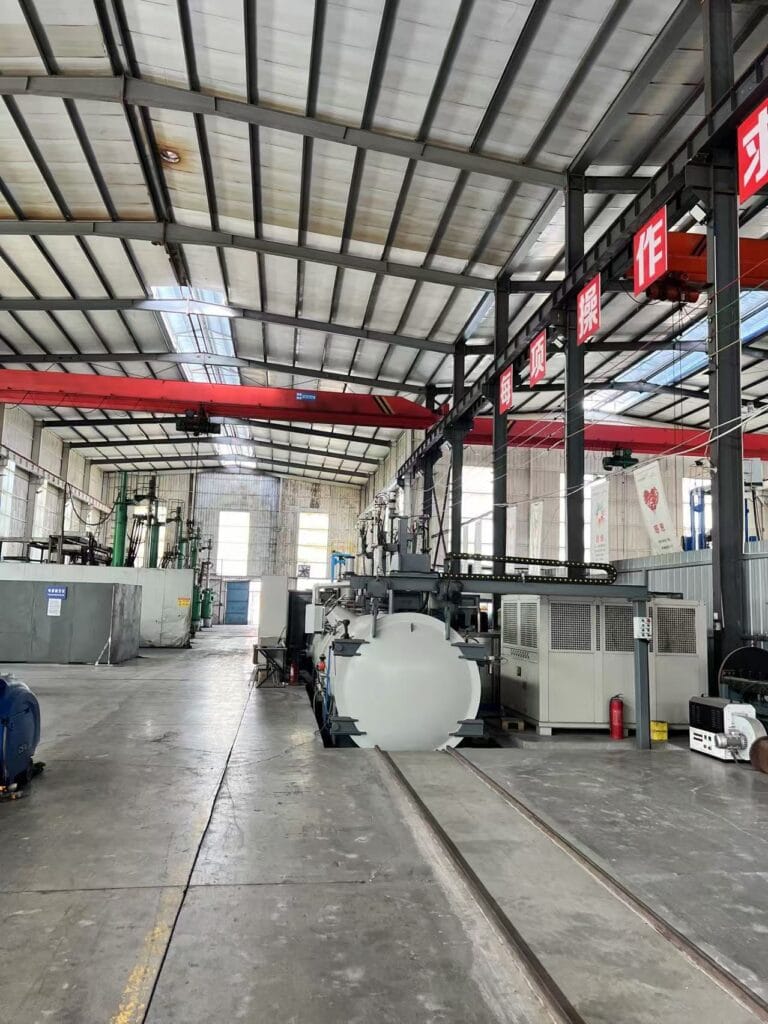
How Are These Advancements Expanding Titanium Applications Across Industries?
As processing techniques advance, titanium ingots are being adopted in more industries and for a wider range of applications.
• Aerospace: High-quality titanium ingots processed through VAR and isothermal forging are used to produce lightweight, durable components like turbine blades and structural parts for aircraft. The improved material properties ensure reliability under extreme conditions.
• Medical: Titanium’s biocompatibility and strength make it ideal for implants and surgical tools. Precision manufacturing techniques allow for the production of highly detailed components, such as dental implants and joint replacements.
• Energy: In power plants, titanium’s corrosion resistance and durability are crucial for components exposed to harsh environments, such as condenser tubes and heat exchangers.
Advancements in processing techniques are enabling titanium ingots to meet the demands of high-performance applications in aerospace, medical, and energy industries.
Claim: Processing Innovations Are Unlocking Titanium’s Full Potential
The integration of advanced melting, forging, and additive manufacturing techniques has significantly enhanced the quality, efficiency, and versatility of titanium ingots. These advancements are enabling manufacturers to expand titanium’s applications in critical industries, from aerospace to medical and energy sectors.
Conclusion: Titanium Processing Techniques Are Shaping the Future of Manufacturing
From my perspective, advancements in titanium ingot processing techniques are driving a new era of manufacturing efficiency and innovation. By improving material quality, reducing costs, and enabling more complex designs, these techniques are unlocking titanium’s full potential as a material of choice for high-performance and precision applications. As these technologies continue to evolve, the role of titanium ingots in manufacturing will only grow, shaping the future of industries worldwide.