Introduction: The Challenges of Marine Environments
Marine applications are among the most demanding environments for materials, with components exposed to high pressures, saltwater corrosion, and dynamic stresses. Titanium forgings, known for their durability, lightweight nature, and exceptional resistance to harsh conditions, have become a preferred choice in this sector. But how exactly do titanium forgings enhance performance in marine applications?
Titanium forgings improve marine performance by providing corrosion resistance, strength, and reliability, ensuring durability and efficiency in subsea and maritime operations.
Let me explain the unique advantages of titanium forgings and their impact on the marine industry.
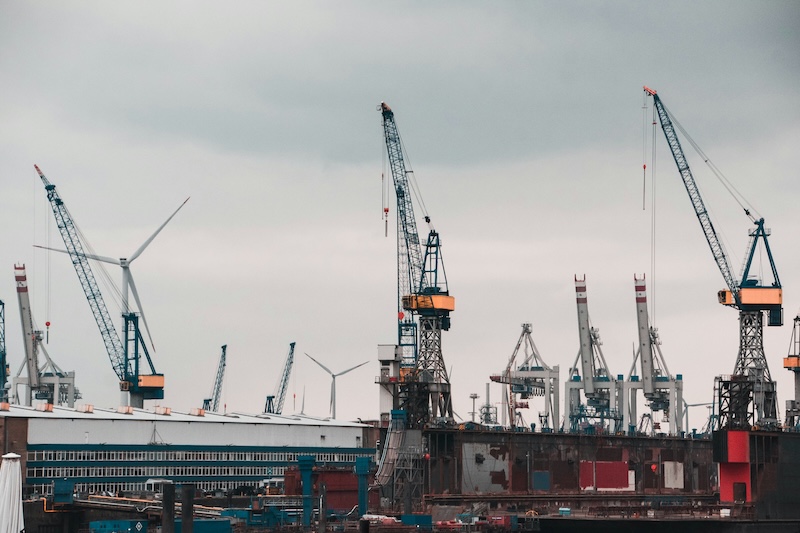
How Does Corrosion Resistance Benefit Marine Applications?
Saltwater is highly corrosive, posing a major challenge for most metals. Titanium’s natural resistance to corrosion makes it an ideal material for marine applications.
Key benefits:
• Oxide Layer Protection: Titanium’s passive oxide layer prevents rust and pitting, even in chloride-rich environments.
• Longevity: Components maintain structural integrity and functionality over decades of exposure.
• Reduced Maintenance: Corrosion-resistant titanium requires fewer repairs, lowering operational costs.
For me, titanium’s resistance to saltwater corrosion is its most significant advantage in ensuring long-lasting marine equipment.
How Does Titanium’s Strength-to-Weight Ratio Improve Efficiency?
In marine applications, reducing weight while maintaining strength is critical for performance and efficiency.
Key advantages:
• Enhanced Vessel Efficiency: Lightweight titanium reduces the overall weight of marine structures, improving fuel economy.
• Load-Bearing Capacity: Despite being light, titanium forgings provide exceptional strength to handle heavy loads and stresses.
• Improved Maneuverability: Reduced weight enhances the agility and performance of ships and underwater equipment.
For me, this combination of strength and lightness ensures titanium forgings contribute to efficient and reliable marine operations.
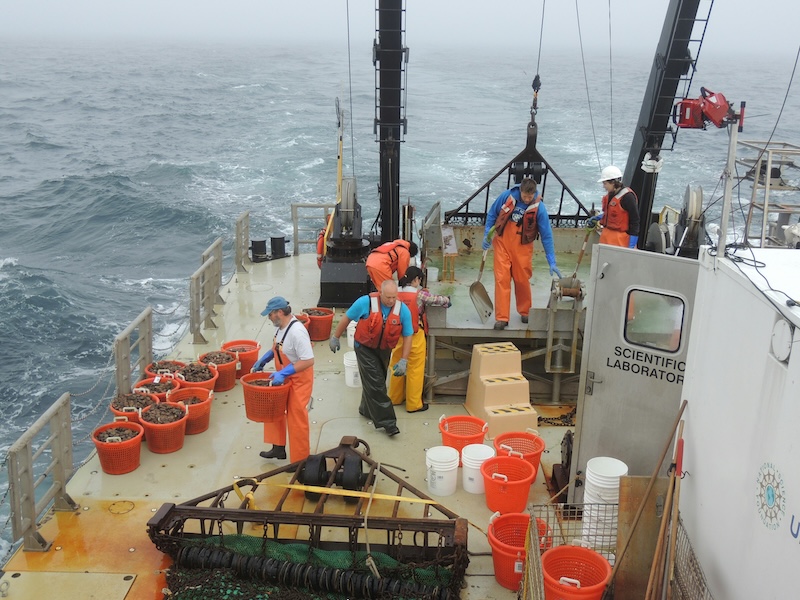
How Do Titanium Forgings Perform Under High Pressure?
Deep-sea environments expose components to extreme pressure, demanding materials that can maintain their integrity.
Key points:
• High Strength: Titanium forgings withstand the crushing forces of deep-sea operations without deforming.
• Fatigue Resistance: Forged titanium resists repeated pressure cycles, ensuring long-term durability.
• Leak Prevention: Components like valves and seals maintain airtight integrity under extreme conditions.
For me, titanium’s ability to endure high-pressure environments ensures the reliability of critical subsea systems.
How Do Titanium Forgings Enhance Subsea Exploration?
Subsea exploration requires advanced materials to build equipment that can withstand the harsh underwater environment.
Applications include:
• Pipelines and Risers: Forged titanium components handle the pressure and corrosion of transporting fluids in deep-sea drilling.
• ROVs and AUVs: Lightweight titanium parts improve the mobility and endurance of remotely operated and autonomous underwater vehicles.
• Connectors and Fasteners: Corrosion-resistant titanium ensures reliable connections in underwater systems.
For me, titanium forgings play a pivotal role in advancing deep-sea exploration and resource extraction technologies.
How Do Titanium Forgings Improve Propulsion Systems?
Marine propulsion systems, including propellers and shafts, benefit significantly from titanium forgings.
Key benefits:
• Corrosion-Free Performance: Propeller shafts made of titanium maintain functionality in saltwater environments.
• Enhanced Lifespan: Forged titanium propellers resist wear and damage, ensuring consistent performance over time.
• Fuel Efficiency: Lightweight propulsion components reduce engine strain, improving overall fuel consumption.
For me, titanium’s role in propulsion systems highlights its ability to enhance efficiency and reduce operational costs.
Why Are Titanium Forgings Essential for Offshore Energy Systems?
Offshore wind farms and oil rigs rely on materials that can withstand harsh marine conditions while ensuring structural integrity.
Key applications:
• Turbine Foundations: Forged titanium components provide durable support for offshore wind turbines.
• Drilling Equipment: Titanium forgings handle the high stresses of offshore oil and gas extraction.
• Corrosion-Resistant Piping: Titanium ensures reliability and safety in transporting fluids in offshore systems.
For me, titanium’s contributions to offshore energy systems demonstrate its versatility and importance in marine technology.
Claim: Why Titanium Forgings Are Indispensable in Marine Applications
Titanium forgings excel in marine applications due to their unparalleled corrosion resistance, strength, and ability to perform under extreme pressures. These qualities ensure durability, efficiency, and reliability across a range of subsea and maritime operations.
Conclusion: Forged for the High Seas
When I think of materials that truly meet the challenges of marine environments, titanium forgings stand out as the gold standard. Their resistance to corrosion, high strength-to-weight ratio, and durability under pressure make them indispensable for subsea exploration, offshore energy, and marine propulsion. For me, titanium forgings represent the future of marine innovation, ensuring that equipment can endure and excel in the harshest conditions the oceans can offer.