Introduction: The Synergy Between Titanium and Advanced Coatings
In high-performance engineering, advanced coatings are applied to materials to enhance properties like wear resistance, corrosion protection, and thermal stability. However, the base material’s compatibility with these coatings is critical to achieving optimal performance. Titanium stands out as an exceptional substrate for advanced coatings. But what makes titanium so compatible?
Titanium’s stable oxide layer, surface chemistry, and structural integrity provide an ideal foundation for advanced coatings, enhancing its already impressive properties.
Let me explain why titanium is a preferred choice for coated applications.
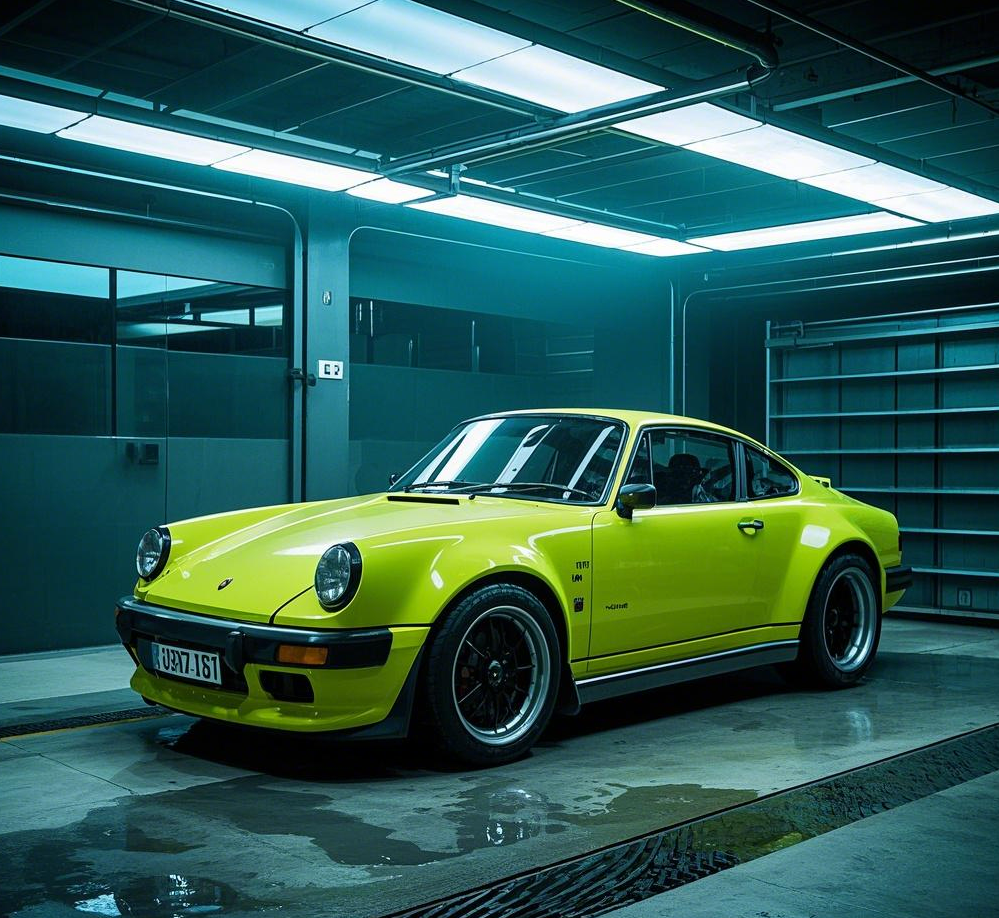
How Does Titanium’s Oxide Layer Facilitate Coating Adhesion?
Titanium naturally forms a thin oxide layer when exposed to air. This layer enhances its compatibility with advanced coatings.
Key advantages include:
• Stable Surface: The oxide layer creates a clean and uniform base for coatings to adhere.
• Self-Healing: If the oxide layer is damaged, it regenerates quickly, maintaining surface integrity.
For me, this natural stability ensures that coatings applied to titanium remain firmly bonded, even in demanding conditions.
How Does Titanium’s Surface Chemistry Support Coating Performance?
Titanium’s low chemical reactivity minimizes unwanted interactions with coating materials during application.
Benefits include:
• Reduced Contamination: Titanium resists surface reactions that can compromise coating adhesion.
• Enhanced Coating Longevity: Stable chemical bonds between titanium and coatings ensure durability over time.
This reactivity balance makes titanium highly compatible with advanced coatings such as ceramic or diamond-like carbon (DLC).
How Does Titanium’s Structural Integrity Improve Coating Durability?
Titanium’s strength and toughness provide a robust foundation that resists deformation and wear, preserving the coating’s functionality.
Advantages include:
• Load-Bearing Capacity: Coatings remain effective on titanium even under mechanical stress.
• Abrasion Resistance: Titanium supports coatings in high-friction environments, reducing wear and tear.
For me, titanium’s structural reliability ensures that coated components maintain peak performance in critical applications.
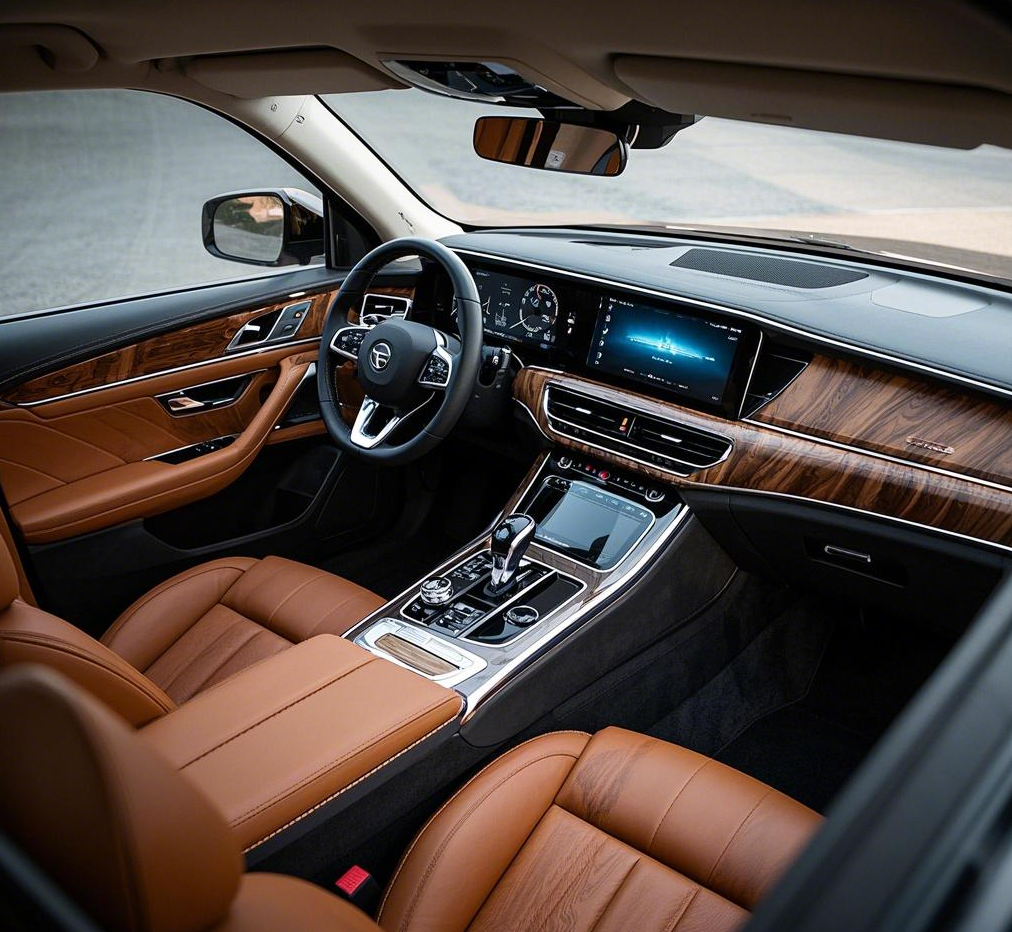
How Do Coatings Enhance Titanium’s Performance?
Advanced coatings amplify titanium’s natural strengths, creating a synergistic effect.
Examples include:
• Wear Resistance: Ceramic or DLC coatings reduce friction and extend the lifespan of titanium parts.
• Thermal Stability: Thermal barrier coatings protect titanium in high-temperature environments like jet engines.
This compatibility allows titanium to meet the specific needs of various industries, from aerospace to medical devices.
How Does Titanium Compare to Other Materials in Coating Compatibility?
Compared to materials like steel and aluminum, titanium’s unique properties make it more suitable for advanced coatings.
• Steel: Prone to corrosion and requires pre-treatment for effective coating adhesion.
• Aluminum: Lightweight but softer and more reactive, limiting coating durability.
• Titanium: Naturally corrosion-resistant and provides a stable surface for coatings, making it the superior choice.
For me, titanium’s compatibility ensures that coatings achieve their full potential, outperforming alternative materials in demanding environments.
What Industries Rely on Coated Titanium Components?
Titanium’s compatibility with coatings makes it invaluable across multiple high-performance sectors:
• Aerospace: Coated titanium fasteners and engine parts resist wear and heat during flight.
• Medical Devices: Titanium implants with biocompatible coatings improve longevity and reduce friction.
• Energy Systems: Coated titanium in turbines and heat exchangers ensures efficiency and durability.
These applications demonstrate how coated titanium pushes the boundaries of innovation and reliability.
Claim: Why Titanium-Coating Compatibility Drives Material Performance
Titanium’s stable oxide layer, surface chemistry, and structural integrity make it uniquely compatible with advanced coatings. This compatibility enhances durability, efficiency, and versatility in high-stress environments.
Conclusion: Titanium’s Role in Coating-Enhanced Engineering
When I think about titanium’s compatibility with advanced coatings, it’s clear that the material and coating work together seamlessly to achieve exceptional results. Titanium not only provides the foundation for coatings to perform optimally but also extends their effectiveness in the toughest conditions. For me, this synergy represents the future of materials science, enabling systems that are more efficient, durable, and tailored to meet the challenges of modern engineering.