Introduction: The Intersection of Titanium Powder and 3D Printing
Customization is the future of manufacturing, especially in industries like healthcare, aerospace, and automotive, where precision and tailored designs are critical. Titanium powder, combined with the power of 3D printing, has emerged as a transformative tool for creating highly customized components. This synergy is reshaping how we approach manufacturing by enabling designs that were previously impossible to achieve.
Titanium powder enables customization through 3D printing by providing a material that is adaptable, strong, and biocompatible, while supporting intricate and patient-specific designs. This innovation allows manufacturers to deliver precision and efficiency across various industries.
Let me share how titanium powder, paired with 3D printing technology, is enabling unparalleled customization and advancing diverse fields.
How Does Titanium Powder Support Complex and Intricate Designs?
Traditional manufacturing methods often struggle with creating complex geometries or internal structures. Titanium powder used in 3D printing overcomes these limitations, enabling intricate designs with precision.
In my experience, titanium powder allows the creation of lattice structures, hollow components, and designs with fine details that are lightweight yet robust. For example, in aerospace, intricate titanium parts reduce weight while maintaining structural integrity, enhancing both performance and fuel efficiency.
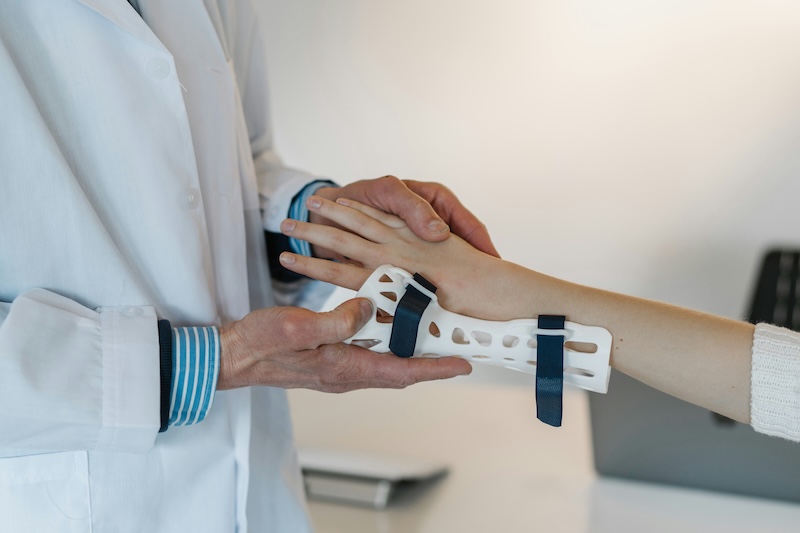
Why Is Titanium Powder Ideal for Patient-Specific Medical Devices?
Medical devices and implants often require customization to fit a patient’s unique anatomy. Titanium powder, combined with 3D printing, makes it possible to produce patient-specific solutions with unmatched precision.
I’ve observed how titanium powder enables the production of custom orthopedic implants, dental prosthetics, and cranial plates tailored to individual patients. This customization improves fit, reduces recovery time, and enhances patient comfort. The biocompatibility of titanium ensures that these devices integrate seamlessly with the body, promoting long-term success.
How Does Titanium Powder Enhance Prototyping and Iterative Design?
3D printing with titanium powder accelerates the prototyping process, allowing manufacturers to quickly produce and test custom designs. This iterative approach ensures that final products meet exact specifications.
For me, the ability to prototype with titanium powder has been invaluable in refining designs for high-performance components. Whether it’s creating aerodynamic parts for the automotive industry or surgical tools for healthcare, rapid prototyping with titanium reduces lead times and improves final outcomes.
How Does Titanium Powder Ensure Material Consistency and Quality in 3D Printing?
The success of 3D printing relies on the uniformity and quality of the material used. Titanium powder is produced with consistent particle size and purity, ensuring reliable performance during printing.
In my work, this consistency has enabled the creation of parts that meet strict industry standards for strength, durability, and safety. Titanium powder’s ability to produce defect-free components makes it ideal for critical applications in industries like aerospace and healthcare, where reliability is non-negotiable.
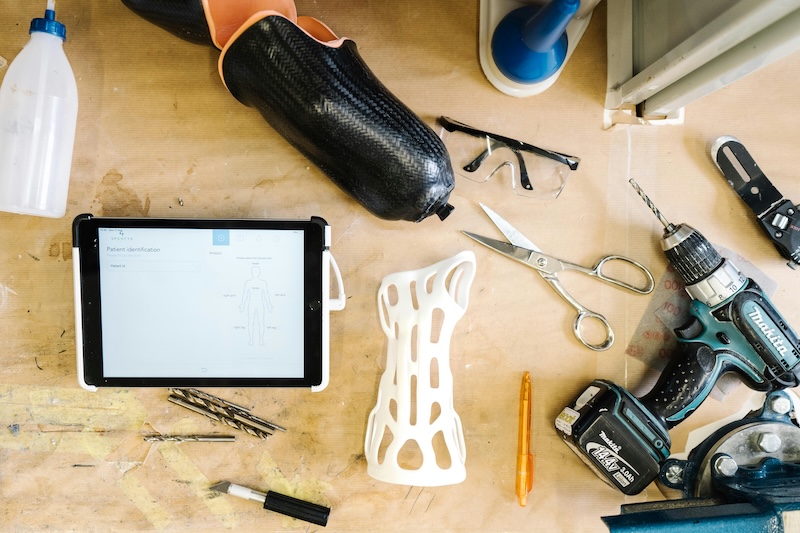
Why Is Titanium Powder a Sustainable Option for Custom Manufacturing?
Sustainability is a growing concern in manufacturing, and titanium powder aligns with this priority. 3D printing minimizes material waste, and titanium’s recyclability ensures an eco-friendly production process.
Using titanium powder, I’ve seen how manufacturers can create customized components with minimal material loss, reducing environmental impact. This efficiency not only supports sustainability goals but also lowers production costs, making titanium powder a practical choice for scalable customization.
Claim: Why Titanium Powder Is Essential for Customization Through 3D Printing
Titanium powder’s adaptability, strength, and biocompatibility make it indispensable for 3D printing applications. Its ability to support intricate designs, patient-specific solutions, and sustainable manufacturing ensures its role in driving innovation across industries.
Conclusion: Titanium Powder and the Future of Custom Manufacturing
Titanium powder, combined with 3D printing, is revolutionizing how industries approach customization. Its unique properties enable the creation of precise, durable, and tailored components that meet the specific needs of diverse applications.
For me, working with titanium powder has been a game-changer in realizing designs that were once impossible. Its potential to create innovative and customized solutions is shaping the future of manufacturing, ensuring that industries remain adaptable and efficient while meeting the evolving demands of consumers and professionals alike.